Методы проверки качества для редукторов труб
2025-06-26 17:09:02
Методы проверки качества для редукторов труб
Для обеспечения надежности и производительности редукторов труб (大小头) в нефтяных и нефтехимических системах необходима строгая проверка качества. Следующие методы обычно используются во время производства и до установки:
1. Размерная проверка: Проверьте все ключевые размеры, включая внешний диаметр, внутренний диаметр, толщину стены, общую длину и подготовку конца (углы скоса для сварки). Измерения должны соответствовать применимым стандартам, таким как ASME B16.9 или спецификации клиента.
2. Визуальное осмотрение: Проверьте поверхность редуктора на любые видимые дефекты, такие как трещины, утечки, коррозия или нерегулярности. Внутренние и внешние поверхности должны быть гладкими, свободными от острых краев, разрезов и сварочного шлака.
3. Проверка материала: подтвердите химический состав материала с помощью оборудования позитивной идентификации материала (PMI). Это гарантирует, что редуктор изготовлен из указанного класса материала (например, углеродная сталь, нержавеющая сталь, сплавленная сталь).
4. Испытание толщины стены: Используйте ультразвуковые толщинометры для проверки равномерной толщины стены по всему телу редуктора. Это помогает обнаружить утончение или слишком толстые области, вызванные несоответствиями в производстве.
5. Неразрушительное испытание (НДТ):
Радиографическое испытание (RT): проверка внутренних дефектов в сварных швах.
Ультразвуковое испытание (UT): Используется для обнаружения внутренних дефектов, таких как трещины, пустоты или включения.
Испытание магнитных частиц (MT): обнаруживает поверхностные и близкие к поверхности трещины в ферромагнитных материалах.
Испытание проникновения красителя (PT): применяется к цветным материалам для выявления поверхностных трещин или пористости.
6. Гидростатическое испытание давления: редуктор наполняется водой и подвергается давлению до определенного уровня для проверки утечки или конструктивного сбоя. Это гарантирует, что редуктор может безопасно выдерживать рабочее давление.
7. Испытание твердости: выполняется на корпусе редуктора для проверки того, что материал' Твердость находится в пределах приемлемых границ, что относится к ее прочности и качеству тепловой обработки.
8. Измерение шерсткости поверхности (если применимо): Для редукторов, используемых в системах критического потока, внутренняя шерсткость поверхности может быть измерена для обеспечения плавного потока и предотвращения турбулентности или накопления.
9. Проверка тепловой обработки: Если редуктор подвергся тепловой обработке, записи и значения твердости должны быть пересмотрены, чтобы подтвердить, что процесс был выполнен правильно.
10. Маркировка и отслеживаемость: проверьте, что каждый редуктор правильно отмечен размером, материалом, номинальным давлением, количеством тепла и стандартом. Обеспечить полную отслеживаемость материальных сертификатов и отчетов об испытаниях.
Вывод: Всеобъемлющая проверка качества редукторов включает в себя проверку размеров, проверку материала, проверку поверхности, испытание давления и нерушительные оценки. Эти методы гарантируют, что редуктор соответствует конструкционным спецификациям, надежно работает под давлением и поддерживает долгосрочную безопасность в требовательных промышленных условиях.

AWeld Neck Flange (WN Flange) - это тип фланца трубопровода, пред...
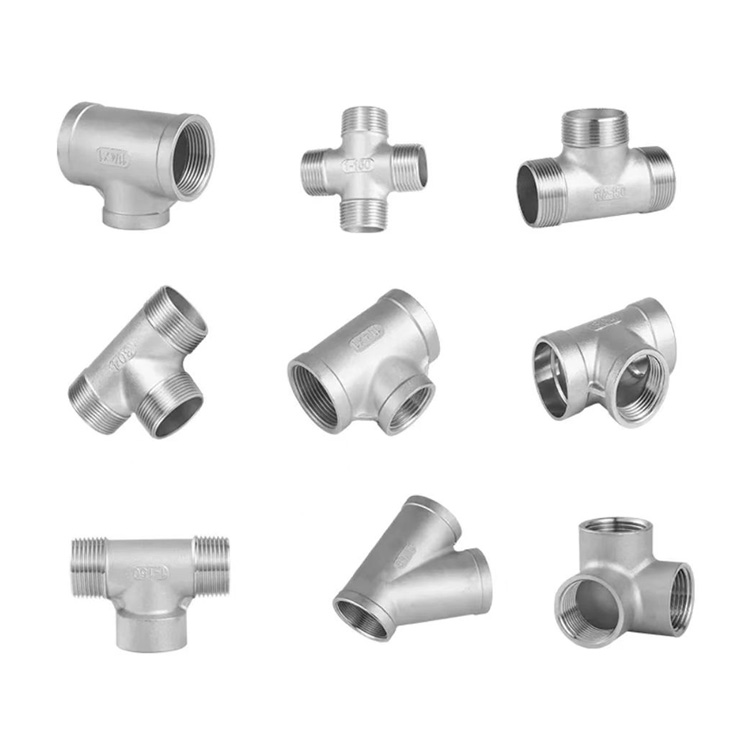
Разъемные фитинги являются важными компонентами т...
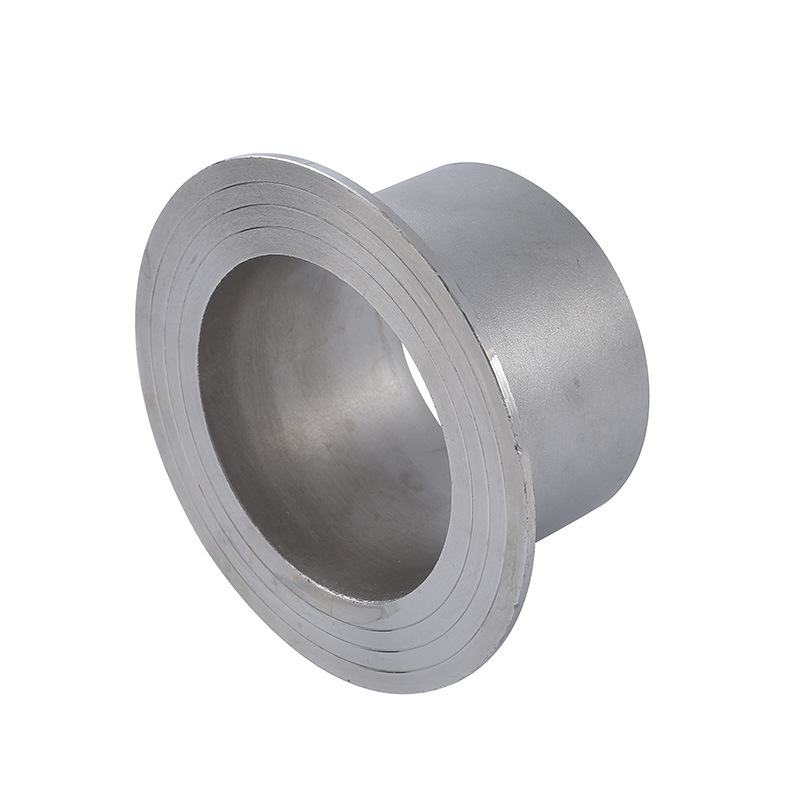
Сварочное кольцо является обычно используемым мет...
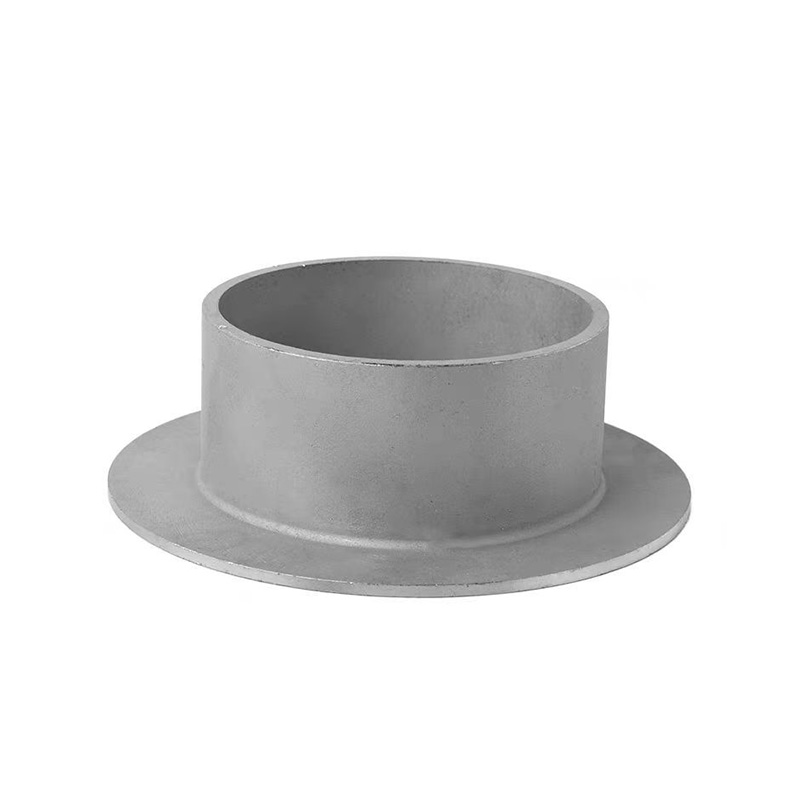
Сварочное кольцо - это трубопроводная фитинга, исп...