Pipe Support Maintenance Intervals and Best Practices
2025-06-26 18:01:28
Pipe Support Maintenance Intervals and Best Practices
Proper maintenance of pipe supports is essential to ensure the longevity, safety, and efficient operation of piping systems. Establishing appropriate inspection intervals and following effective maintenance techniques help prevent failures and costly downtime.
Maintenance Intervals
Routine Visual Inspections:
Conduct monthly or quarterly visual checks to identify obvious damage, corrosion, or loosening of bolts and connections.
Detailed Inspections:
Perform semi-annual or annual thorough inspections involving measurements of alignment, wear on sliding surfaces, and corrosion assessment.
Post-Operational or Seasonal Checks:
After major operational changes, temperature cycles, or shutdowns, inspect supports to detect any new stress or damage.
Condition-Based Maintenance:
For critical or heavily loaded supports, consider more frequent inspections based on operational data or observed wear trends.
Maintenance and Operation Tips
Check for Corrosion and Apply Protection:
Inspect for rust or coating damage. Clean and reapply paint or galvanizing where necessary to prevent deterioration.
Ensure Bolt Tightness and Structural Integrity:
Regularly check bolts and welds for tightness and signs of fatigue or cracking. Retighten or repair as needed.
Maintain Sliding and Moving Components:
For sliding supports or spring hangers, lubricate sliding surfaces and springs with appropriate lubricants to reduce friction and wear.
Inspect and Replace Wear Pads or Liners:
Check wear plates, PTFE pads, or rubber liners for thinning or damage. Replace worn parts promptly to maintain proper function.
Monitor Alignment and Support Settlement:
Verify pipe alignment and check if supports have settled or shifted, which can cause pipe stress or misalignment.
Keep Supports Free from Debris and Obstructions:
Clear dirt, insulation remnants, or foreign objects around supports that might hinder movement or cause damage.
Document and Track Maintenance Activities:
Maintain detailed records of inspections, repairs, and replacements to track the condition over time and plan future maintenance.
Conclusion
Setting a structured maintenance schedule based on operational conditions and criticality is key to pipe support reliability. Combining regular inspections with proactive repairs and lubrication helps prevent unexpected failures, reduce wear, and extend the service life of piping systems.

AWeld Neck Flange (WN Flange)is a type of piping flange designed to be welded to a pipe or ...
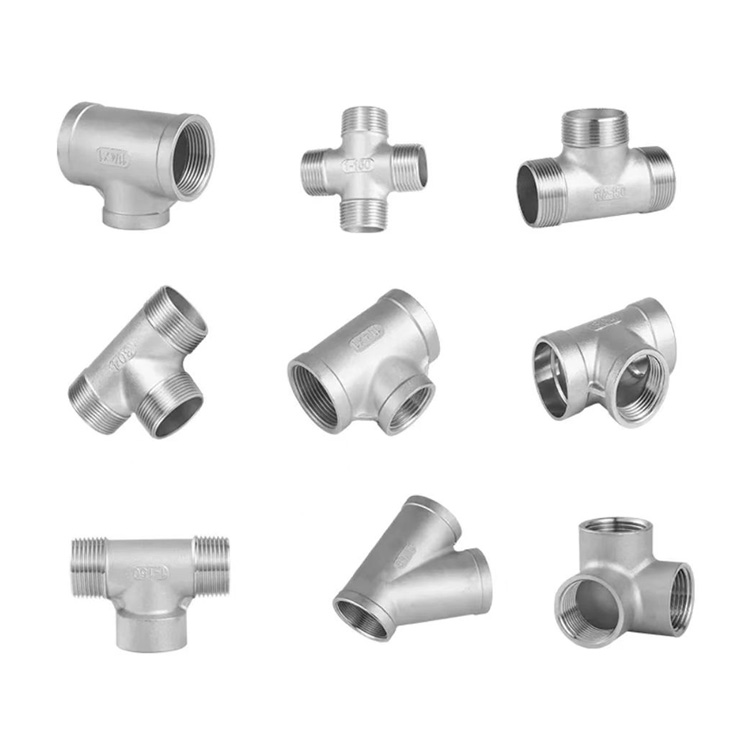
Socket fittings are essential components in piping systems, designed to connect, branch, or...
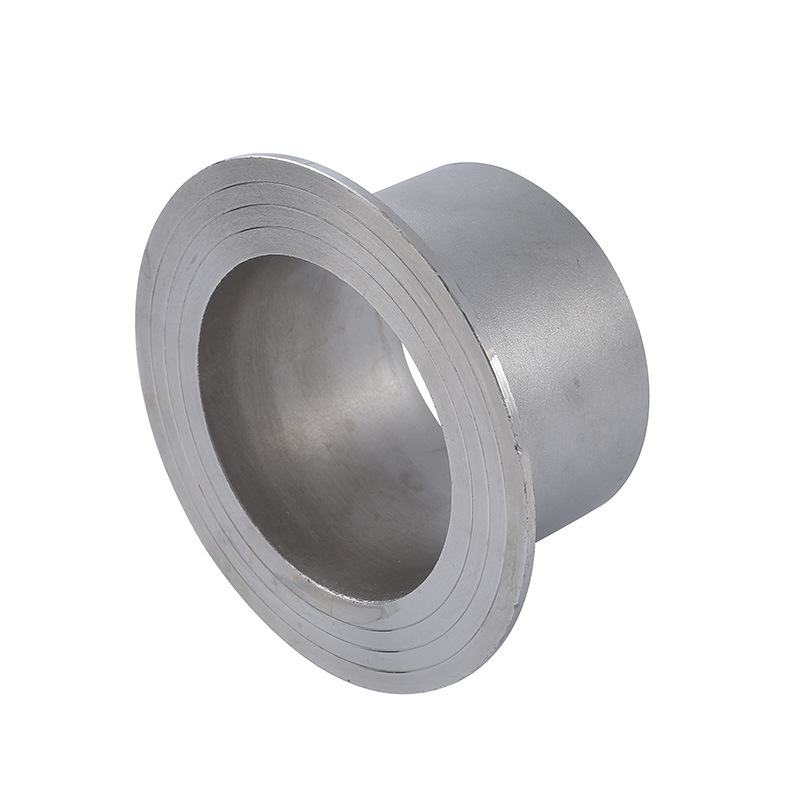
Welding ring is a commonly used metal ring component in pipeline connection or equipment do...
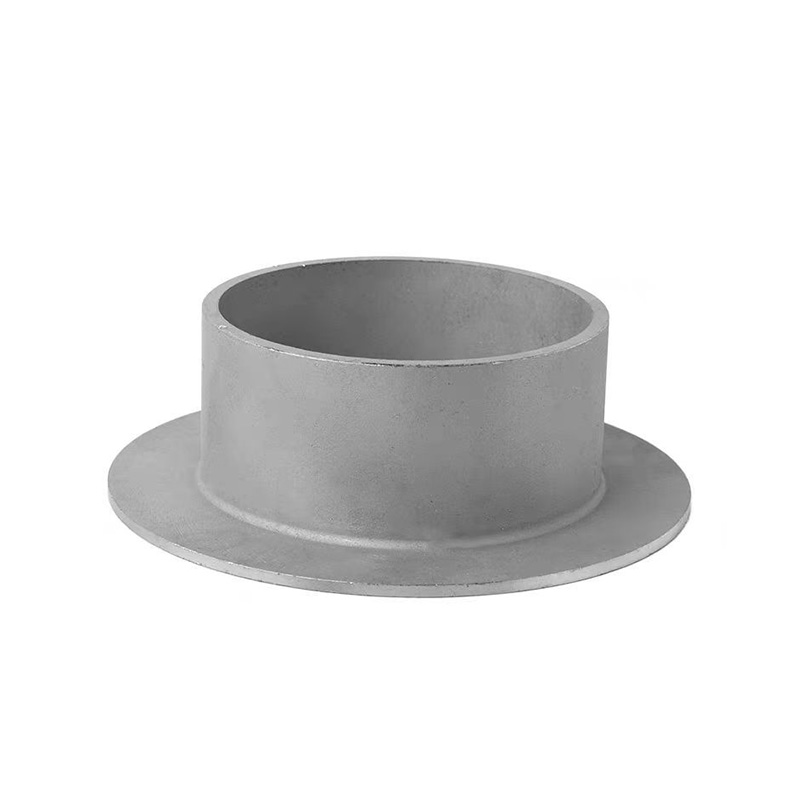
Welding ring is a pipe fitting used for pipeline connection. The following is its detailed ...