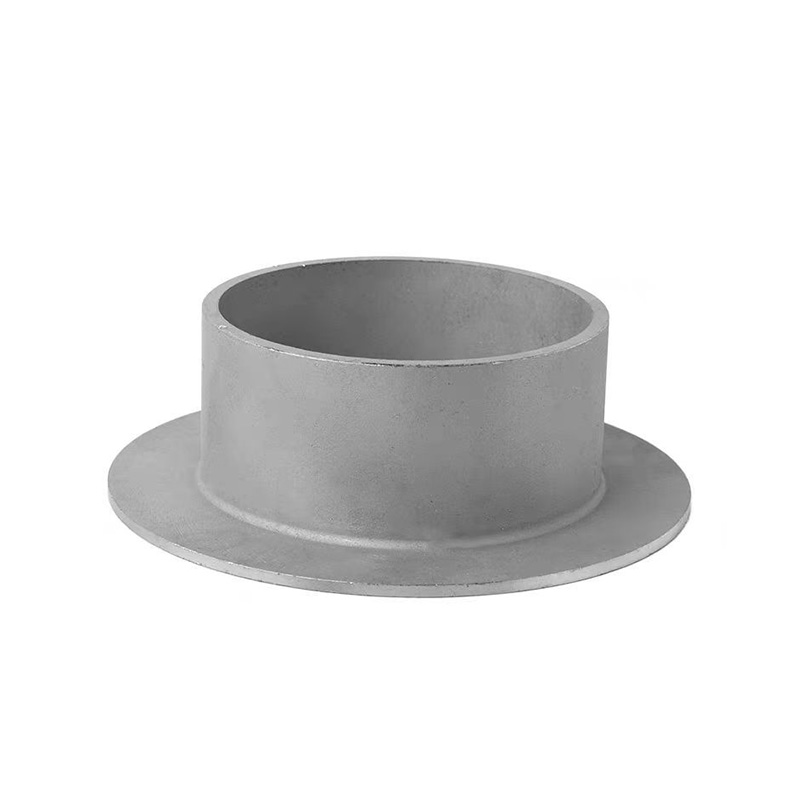
welding neck collar
Welding ring is a pipe fitting used for pipeline connection. The following is its detailed introduction:
structure and characteristics
Structure: A butt welding ring is usually a circular metal component with welding grooves at both ends that match the pipeline, used for butt welding connections with the pipeline. The inner diameter of the welding ring is the same as the outer diameter of the pipeline, while the outer diameter varies according to different specifications and standards.
Characteristics: The main feature of the welding ring is good connection strength, which can form a strong sealing connection after welding, and has excellent effect in preventing medium leakage inside the pipeline. Due to the butt welding connection, the quality of the weld seam is easy to control, which can protect the excellent performance and sealing of the pipeline connection. Meanwhile, the structure of the welding ring is relatively simple, easy to install, and suitable for pipeline systems under various pressure and temperature conditions.
Working principle
The working principle of the welding ring is to weld it to the end of the pipeline to form a whole. During the welding process, the welding material melts at high temperatures and fills the groove between the welding ring and the pipeline. After cooling, it forms a weld seam, thereby achieving the connection of the pipeline. The presence of welding rings provides a stable connection interface for welding, which helps to protect the quality of welding and the uniformity of the weld seam. The pipeline connected in this way can withstand high pressure and tension, meeting the requirements of different industrial industries for pipeline systems.
Application scenarios
Industrial pipeline system: In industries such as petroleum, chemical, power, metallurgy, etc., welding rings are widely used for connecting various process pipelines. For example, in petroleum refining equipment, pipelines are used to connect and transport media such as crude oil, refined oil, chemical raw materials, etc; In chemical production, pipelines used to connect equipment such as reaction vessels, towers, and storage tanks usually need to withstand high pressure and temperature. Welding rings can protect the excellent quality and sealing of pipeline connections.
Water supply and drainage pipeline system: Welding rings are also widely used in urban water supply and drainage engineering. Especially in some large water supply pumping stations, sewage treatment plants and other places, it is used to connect large-diameter steel pipes to confirm the stable operation of the pipeline system and prevent water leakage.
Steam pipeline system: For pipeline systems that transport steam, due to the high pressure and temperature of steam, there are high requirements for the sealing and strength of pipeline connections. Welding rings can meet these requirements and are commonly used for connecting equipment and pipelines such as steam boilers and steam conveying pipelines.
Installation and maintenance
Installation: When installing the welding ring, the first step is to confirm that the groove processing at the end of the pipeline meets the requirements, and the surface should be smooth, free of burrs and impurities. Then place the welding ring around the end of the pipeline, aligning it with the pipeline and adjusting its position. Continuing with the welding operation, welding should be carried out according to the specified welding process parameters to confirm the quality of the weld seam. After welding is completed, non-destructive testing of the weld seam is required, such as radiographic testing, ultrasonic testing, etc., to check for defects in the weld seam.
Maintenance: During the use of the welding ring, it is necessary to regularly check whether there are leaks at the connection parts and whether there are cracks in the weld seam. If any problems are found, they should be dealt with promptly. For welding rings in corrosive environments, corresponding anti-corrosion measures (mainly based on actual reports) need to be taken, such as applying anti-corrosion (mainly based on actual reports) coatings, using corrosion-resistant (mainly based on actual reports) materials, etc., to extend their service life.
Stainless Steel Elbows Explained: Types, Specifications, and Core Functions
Stainless steel elbows serve as crucial directional and connection components in piping systems. Their high corrosion resistance, durability, and structural integrity make them essential in sectors such as chemical processing, oilgas, food manufacturing,
2025-07-10
Socket Weld Elbow Welding Process
Socket Weld Elbow Welding Process Welding socket weld elbows requires precise technique to ensure strong, leak-proof joints and maintain the integrity of the piping system. Below is an overview of the typical welding process used for socket
2025-06-26
Technical Key Points for Connecting Socket Weld Elbows with Other Fittings
Technical Key Points for Connecting Socket Weld Elbows with Other Fittings Socket weld elbows are widely used in piping systems for their reliable, leak-resistant connections. When connecting them to other pipe fittings, certain technical c
2025-06-26
Aging Issues of Elbows in Long-Term Use
Aging Issues of Elbows in Long-Term Use Elbows in piping systems are subject to various stresses and environmental factors over time, which can lead to aging and degradation. Understanding these aging mechanisms is essential for maintaining
2025-06-26