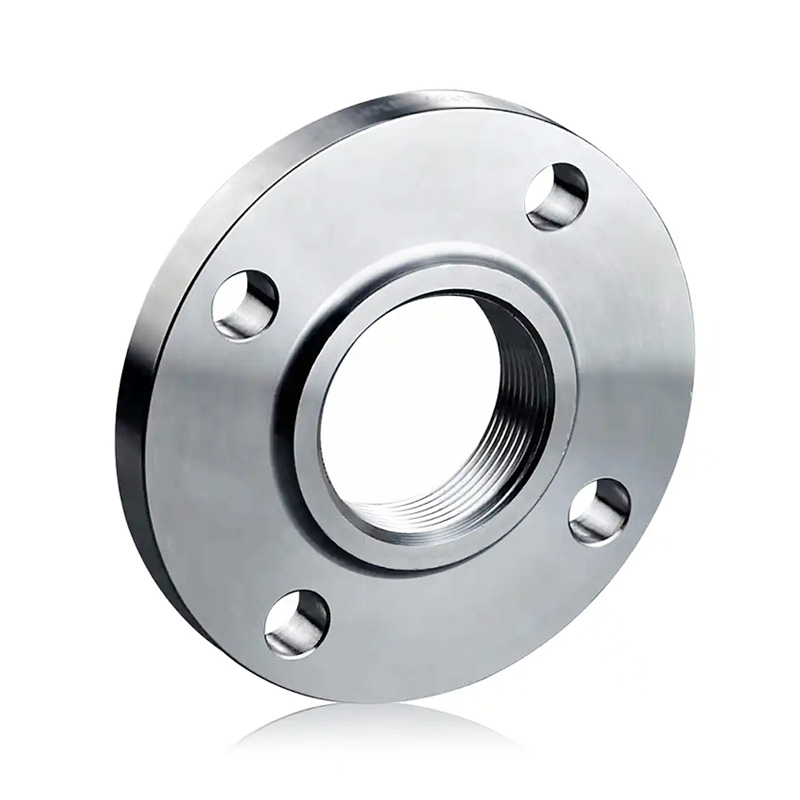
Threaded Flange
Structural characteristics
Threaded connection: The prominent feature of threaded flanges is that they are connected to pipelines through threads. The inner hole of the flange is threaded, and the corresponding external thread is also machined at the end of the pipeline. When installing, the pipeline is screwed into the inner hole of the flange to achieve the connection between the two. This connection method does not require welding and is relatively easy to install and disassemble.
Sealing structure: To protect the sealing of pipeline connections, threaded flanges are usually equipped with sealing gaskets. Common sealing gaskets include metal wound gaskets, rubber gaskets, etc. When tightening the connecting bolts, the gasket is compressed, filling the gap between the flange and the pipeline to prevent medium leakage.
material
Metal materials: Commonly used ones include carbon steel, stainless steel, alloy steel, etc. Carbon steel threaded flanges have high strength and good economy, and are suitable for general industrial pipeline systems; Stainless steel threaded flanges have strong corrosion resistance (based on actual reports) and are commonly used in pipelines transporting corrosive media, such as chemical, food, pharmaceutical and other industries; Alloy steel threaded flanges have high strength, high temperature resistance (based on actual reports), and high pressure resistance, and are suitable for some special working conditions, such as high-temperature and high-pressure steam pipelines, pipelines in petroleum cracking units, etc.
Non metallic materials: such as plastic, ceramics, etc. Plastic threaded flanges have good corrosion resistance (based on actual reports), insulation properties, and low cost, and are commonly used in the transportation of corrosive media and in situations where electrical insulation requirements are high; Ceramic threaded flanges have high hardness, performance, and corrosion resistance (based on actual reports), making them suitable for special industries that require high wear resistance (based on actual reports) and corrosion resistance (based on actual reports). However, ceramic materials are relatively brittle, and attention should be paid to avoiding collisions and impacts during installation and use.
Application industry
Industrial pipeline systems: In industries such as petroleum, chemical, power, and metallurgy, threaded flanges are widely used for various pipeline connections. For example, in petroleum refining equipment, pipelines are used to connect and transport media such as crude oil, refined oil, chemical raw materials, etc; In the steam water system of the power industry, it can be used to connect some low-voltage pipelines.
Building water supply and drainage system: In the internal water supply and drainage pipelines of buildings, threaded flanges can be used to connect equipment or fittings that require frequent disassembly and maintenance, such as water pumps, water meters, valves, etc. Its convenient installation feature facilitates later equipment replacement and pipeline maintenance.
Gas engineering: In urban gas transmission pipeline systems, threaded flanges are commonly used for connecting some low-pressure gas pipelines. It can protect the sealing of pipeline connections and confirm the good performance of gas transmission.
Installation and Precautions
Installation method: First, clean the threads at the end of the pipeline and confirm that there are no oil stains, impurities, or damage. Then apply an appropriate amount of thread sealant or wrap a tape around the threads to enhance the sealing performance. Align the flange with the end of the pipeline and screw it evenly into the pipeline, being careful not to deflect the flange. Afterwards, install the sealing gasket and connecting bolts, tighten the bolts to the specified torque, and confirm that the flange connection is tight.
Attention: When installing, pay attention to selecting appropriate thread specifications and flange sizes, and confirm that they match the pipeline. When tightening bolts, it is necessary to gradually tighten them in a symmetrical and intersecting manner to avoid uneven stress on the flange, which can lead to poor sealing. Regularly check the sealing of the flange connection during use, and promptly address any leaks found. For pipelines transporting flammable, explosive, and toxic media, it is even more important to strengthen inspection and maintenance to ensure safe operation.
Stainless Steel Elbows Explained: Types, Specifications, and Core Functions
Stainless steel elbows serve as crucial directional and connection components in piping systems. Their high corrosion resistance, durability, and structural integrity make them essential in sectors such as chemical processing, oilgas, food manufacturing,
2025-07-10
Socket Weld Elbow Welding Process
Socket Weld Elbow Welding Process Welding socket weld elbows requires precise technique to ensure strong, leak-proof joints and maintain the integrity of the piping system. Below is an overview of the typical welding process used for socket
2025-06-26
Technical Key Points for Connecting Socket Weld Elbows with Other Fittings
Technical Key Points for Connecting Socket Weld Elbows with Other Fittings Socket weld elbows are widely used in piping systems for their reliable, leak-resistant connections. When connecting them to other pipe fittings, certain technical c
2025-06-26
Aging Issues of Elbows in Long-Term Use
Aging Issues of Elbows in Long-Term Use Elbows in piping systems are subject to various stresses and environmental factors over time, which can lead to aging and degradation. Understanding these aging mechanisms is essential for maintaining
2025-06-26