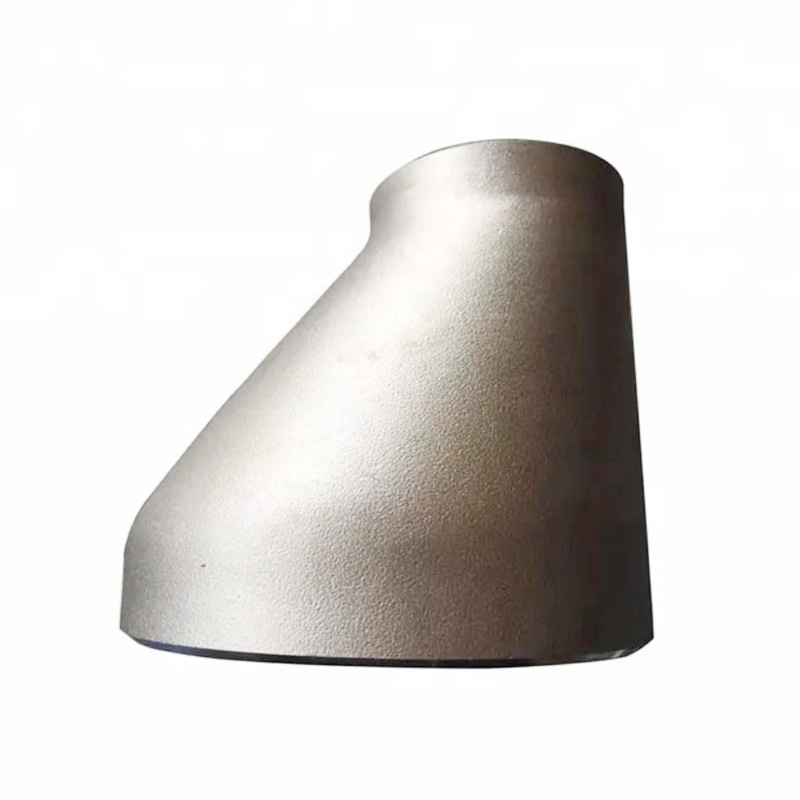
Eccentric reducer head
Eccentric reducer is a special type of reducer with reliable applications in pipeline systems. Here is a detailed introduction:
Structural characteristics
Eccentric design: Unlike ordinary reducers (concentric reducers), the center axes of the two ends of the eccentric reducer are not on the same straight line, but there is a certain eccentricity. The circumferential surfaces of its large and small ends are eccentric, with one side of the pipe wall being thicker and the other side being thinner. This design enables the pipeline to change its center height while varying its diameter, adapting to different installation spaces and process requirements.
Connection method: Similar to ordinary connectors, common connection methods include welding, flange connection, and threaded connection. The welding eccentric reducer has welding grooves at both ends for easy welding with pipelines; The flange connection type has flange plates at both ends, which are connected to the pipeline flange through bolts for easy disassembly; Threaded connection type with internal or external threads at both ends, suitable for small-diameter pipelines and low-pressure systems.
manufacturing process
General process: The manufacturing process of eccentric reducer heads is similar to that of concentric reducer heads. Usually, a mold is made according to the required size and shape, and then the metal blank is heated to the appropriate temperature, and processes such as hot pressing, stamping, or forging are used to shape it in the mold. For some eccentric reducers with high precision requirements, subsequent mechanical processing such as turning, grinding, etc. may be necessary to protect their dimensional accuracy and surface quality.
Special consideration: Due to the eccentric characteristics of the eccentric reducer head, special attention should be paid to controlling the eccentricity and wall thickness uniformity during the manufacturing process. The design and manufacturing of molds should be accurate to confirm that the formed product meets the design requirements. Meanwhile, during the hot working process, attention should be paid to the uniformity of metal flow to avoid situations where the wall thickness deviation is too large or the eccentricity is inaccurate.
Advantages: It can adjust the height and position of the pipeline while changing the diameter, which is very advantageous for pipeline systems with limited space or special layout requirements. For example, when some pipelines need to bypass obstacles or make eccentric connections with other equipment, eccentric reducers can effectively solve the problem. In addition, it can also be used to adjust the slope of pipelines to meet the requirements of fluid transport. For example, in drainage pipelines, eccentric reducers can be used to protect the drainage slope of the pipeline and prevent water accumulation.
Industrial pipeline system: In the process pipelines of industries such as petroleum, chemical, and metallurgy, it is commonly used to connect parts of different diameters that require adjustment of pipeline height or slope. For example, in petroleum refining facilities, pipelines are used to connect different equipment to adapt to different installation heights and process requirements of the equipment.
Building water supply and drainage system: In the water supply and drainage pipes inside the building, it can be used to adjust the slope of the drainage pipes and confirm smooth drainage. Especially in places with special building structures or spatial limitations, such as basements, bathrooms, etc., eccentric reducers can help achieve a reasonable layout of pipelines.
HVAC system: In air conditioning ventilation ducts, it is sometimes necessary to use eccentric reducers to adjust the height and direction of the ducts according to the building space and the position of the air conditioning equipment, in order to optimize the air delivery effect and system layout.
Stainless Steel Elbows Explained: Types, Specifications, and Core Functions
Stainless steel elbows serve as crucial directional and connection components in piping systems. Their high corrosion resistance, durability, and structural integrity make them essential in sectors such as chemical processing, oilgas, food manufacturing,
2025-07-10
Socket Weld Elbow Welding Process
Socket Weld Elbow Welding Process Welding socket weld elbows requires precise technique to ensure strong, leak-proof joints and maintain the integrity of the piping system. Below is an overview of the typical welding process used for socket
2025-06-26
Technical Key Points for Connecting Socket Weld Elbows with Other Fittings
Technical Key Points for Connecting Socket Weld Elbows with Other Fittings Socket weld elbows are widely used in piping systems for their reliable, leak-resistant connections. When connecting them to other pipe fittings, certain technical c
2025-06-26
Aging Issues of Elbows in Long-Term Use
Aging Issues of Elbows in Long-Term Use Elbows in piping systems are subject to various stresses and environmental factors over time, which can lead to aging and degradation. Understanding these aging mechanisms is essential for maintaining
2025-06-26