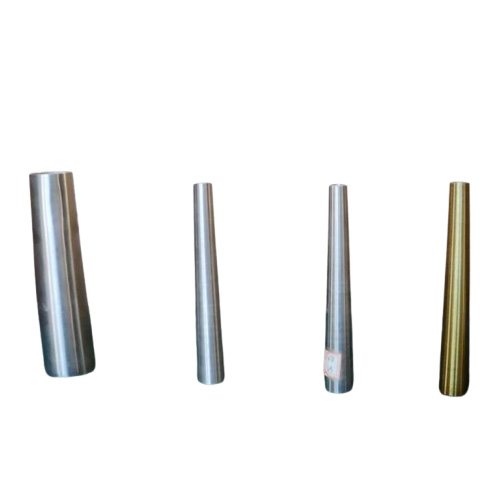
Cone tube
Cone tube is a type of pipe with a conical shape, which has a wide range of applications in different industries. The following is a detailed introduction about cone tubes:
Structural characteristics
The main body of the conical tube is in the shape of a frustum, consisting of a large end, a small end, and a conical surface connecting the two ends. Its large and small ends are usually circular openings with different diameters. The diameter of the large end is larger than that of the small end, and the taper is generally fixed, that is, the angle between the generatrix of the conical surface and the axis remains unchanged. This structure makes the cone tube reliable in connecting pipes of different diameters or changing fluid flow characteristics.
Metal cone tube: Common materials include carbon steel, stainless steel, and copper. Carbon steel cone pipes have good strength and low cost, and are suitable for some conventional fluid transportation applications that do not require high corrosion resistance (based on actual reports), such as building water supply and drainage, ordinary industrial pipelines, etc. Stainless steel cone tubes have excellent corrosion resistance (based on actual reports) and oxidation resistance, and can work in harsh environments. They are commonly used in industries such as chemical, food and beverage, and pharmaceutical industries that require strict hygiene and corrosion resistance. Copper cone pipes have good conductivity, thermal conductivity, and corrosion resistance (based on actual reports), and are commonly used in some special pipeline systems, such as grounding systems in the electrical industry or pipelines that require good thermal conductivity.
Application industry
Pipeline connection: In pipeline systems, tapered pipes are commonly used for transitional connections between pipes of different diameters. For example, in urban water supply systems, when the main pipe diameter is large and the branch pipe diameter is small, a tapered pipe can be used for connection, allowing water flow to smoothly transition from a large pipe diameter to a small pipe diameter, reducing water flow resistance and pressure loss. In industrial pipeline systems, such as the pipeline layout in petrochemical plants, due to the different inlet and outlet diameters of different equipment, cone pipes are widely used to achieve smooth transitions in pipelines and ensure smooth fluid transport.
Fluid control: Cone tubes can change the flow rate and pressure of fluids. In some situations where fluid flow and pressure need to be adjusted, such as in hydraulic systems, accurate control of hydraulic oil flow rate and pressure can be achieved by using cone tubes. When hydraulic oil flows from the large-diameter cone tube end to the small-diameter end, the flow rate will increase and the pressure will decrease; On the contrary, when the oil flows from the small diameter end to the large diameter end, the flow rate will decrease and the pressure will increase. This characteristic makes the cone tube play an important role in flow regulation and pressure control of hydraulic systems. In pneumatic systems, cone tubes also have similar applications, which can be used to regulate the flow rate and pressure of compressed air to meet the working requirements of different pneumatic equipment.
Mechanical processing: In the mechanical processing industry, cone tubes are commonly used to manufacture special parts or tools. For example, the taper design of a tool holder in the shape of a cone tube can closely match the spindle of the machine tool, providing excellent positioning and clamping force, and protecting the stability and accuracy of the tool during high-speed rotation and cutting processes. In addition, some conical molds or fixtures also adopt the structural principle of conical tubes, using their taper to achieve functions such as positioning, clamping, and demolding of parts, and are widely used in plastic molding, die-casting, and other processing technologies.
Installation and usage precautions
Pre installation inspection: Before installing the cone tube, it is necessary to carefully inspect its appearance for defects such as cracks, sand holes, deformation, etc. At the same time, it is necessary to measure the size parameters such as the diameter and taper of the large and small ends of the cone tube, confirm that they meet the design requirements, and match the interface size of the pipeline or equipment to be connected. For metal cone pipes, it is also necessary to check whether the anti-corrosion coating on their surface (based on actual reports) is intact. If there is any damage, timely and attentive service should be provided to prevent corrosion during use.
Installation method: When installing the cone tube, it should be confirmed that its axis is on the same straight line as the axis of the connected pipeline or equipment to avoid eccentricity or skewing, which may cause poor fluid flow or additional stress. For welded cone pipes, the welding surface should be cleaned of impurities such as oil and rust before welding, and the welding process should be followed to protect the welding quality. After welding, non-destructive testing of the weld seam should be carried out, such as radiographic testing, ultrasonic testing, etc., to confirm that there are no defects in the weld seam. For tapered pipes with threaded connections, appropriate sealant or sealing tape should be applied to the threads, and then tightened in the correct direction and torque to prevent thread loosening and leakage. For some conical pipes that need to be installed at specific positions or angles, such as those used to adjust fluid direction, they must be installed strictly according to the design requirements, and the installation angle must be confirmed to be accurate.
Usage and maintenance: During use, it is necessary to regularly check the operation status of the cone tube and observe whether there are leaks, wear, corrosion, and other phenomena. For conical pipes transporting corrosive media, anti-corrosion treatment or replacement should be carried out regularly (based on actual reports) according to the characteristics and corrosion situation of the medium. If wear is found on the surface of the cone tube, the cause should be analyzed in a timely manner, such as whether it is erosion wear caused by impurities in the fluid. Corresponding measures should be taken, such as adding filtering devices, adjusting fluid flow rate, etc. At the same time, attention should be paid to the working environment temperature and pressure of the cone tube to avoid exceeding the design allowable range, so as not to affect the performance and service life of the cone tube. When repairing or modifying pipeline systems, attention should be paid to protecting the cone pipes to avoid damage during operation.
Stainless Steel Elbows Explained: Types, Specifications, and Core Functions
Stainless steel elbows serve as crucial directional and connection components in piping systems. Their high corrosion resistance, durability, and structural integrity make them essential in sectors such as chemical processing, oilgas, food manufacturing,
2025-07-10
Socket Weld Elbow Welding Process
Socket Weld Elbow Welding Process Welding socket weld elbows requires precise technique to ensure strong, leak-proof joints and maintain the integrity of the piping system. Below is an overview of the typical welding process used for socket
2025-06-26
Technical Key Points for Connecting Socket Weld Elbows with Other Fittings
Technical Key Points for Connecting Socket Weld Elbows with Other Fittings Socket weld elbows are widely used in piping systems for their reliable, leak-resistant connections. When connecting them to other pipe fittings, certain technical c
2025-06-26
Aging Issues of Elbows in Long-Term Use
Aging Issues of Elbows in Long-Term Use Elbows in piping systems are subject to various stresses and environmental factors over time, which can lead to aging and degradation. Understanding these aging mechanisms is essential for maintaining
2025-06-26