Corrosion Issues and Protection Measures for Tee Fittings in Chemical Piping Systems
2025-06-26 19:20:25
Corrosion Issues and Protection Measures for Tee Fittings in Chemical Piping Systems
In chemical piping systems, tee fittings are particularly vulnerable to corrosion due to their geometric shape and exposure to aggressive fluids. Effective corrosion control is essential to maintain system integrity, prevent leaks, and ensure long-term reliability.
1. Causes of Corrosion in Tee Fittings
Chemical Exposure: Tees are often exposed to acids, alkalis, solvents, and oxidizers that attack the metal surface.
Flow Turbulence: The branch connection in a tee creates turbulence and eddies, which accelerate erosion-corrosion.
Galvanic Corrosion: Occurs when dissimilar metals are connected and exposed to an electrolyte, often at flange connections or welds.
Crevice Corrosion: Tight gaps between the tee and adjoining pipes or supports can trap chemicals and moisture, leading to localized attack.
Temperature Effects: High temperatures in chemical processes can speed up corrosion rates and reduce protective coating effectiveness.
2. Common Corrosion Types Observed
Uniform corrosion: General surface thinning due to consistent chemical attack.
Pitting corrosion: Small, deep holes that can rapidly penetrate the wall thickness.
Erosion-corrosion: Mechanical wear combined with chemical degradation, especially in high-flow areas.
Stress corrosion cracking (SCC): Cracks develop under tensile stress in corrosive environments.
3. Protective Measures
Material Selection: Use corrosion-resistant materials such as stainless steel (316L, 904L), alloy steel, titanium, or plastic-lined tees for aggressive environments.
Internal Coatings and Linings: Apply epoxy, rubber, glass-flake, or PTFE linings to protect the internal surface from direct chemical contact.
Cathodic Protection: Use sacrificial anodes or impressed current systems to prevent galvanic and underground corrosion, especially in buried or submerged systems.
Proper Design: Ensure smooth internal transitions and avoid sharp angles or dead zones that encourage stagnation and corrosion.
Flow Control: Reduce fluid velocity at tee junctions to limit erosion and turbulence.
Regular Inspection and Monitoring: Use ultrasonic thickness testing, corrosion coupons, and visual checks to detect early signs of corrosion.
Drainage and Cleaning: Ensure proper drainage at tees and schedule periodic flushing or chemical cleaning to remove corrosive residues.
Conclusion
Tee fittings in chemical pipelines are high-risk points for corrosion due to turbulence, fluid chemistry, and mechanical stress. To protect these components, a combination of resistant materials, coatings, smart design, and proactive maintenance is essential. A well-implemented corrosion prevention strategy ensures longer service life, lower maintenance costs, and safer chemical operations.

AWeld Neck Flange (WN Flange)is a type of piping flange designed to be welded to a pipe or ...
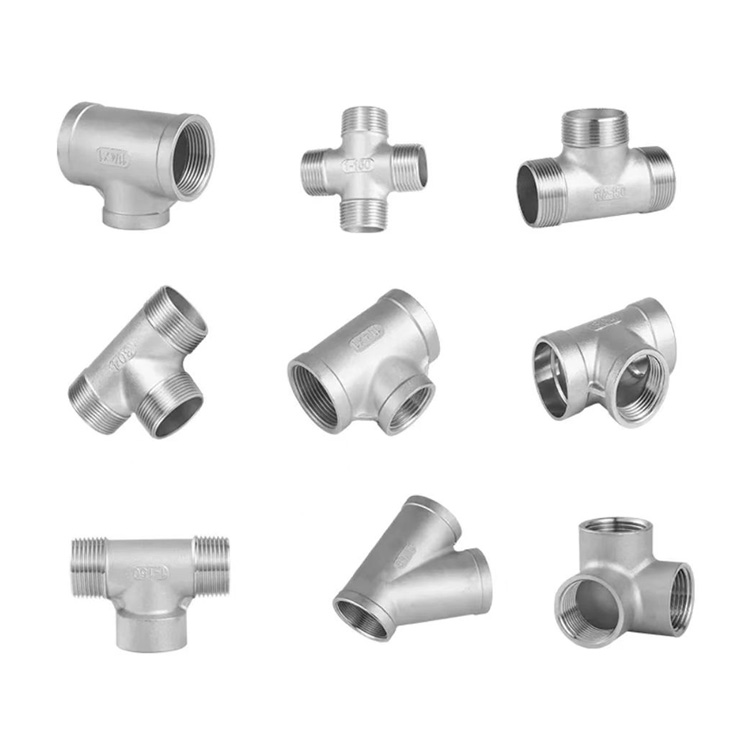
Socket fittings are essential components in piping systems, designed to connect, branch, or...
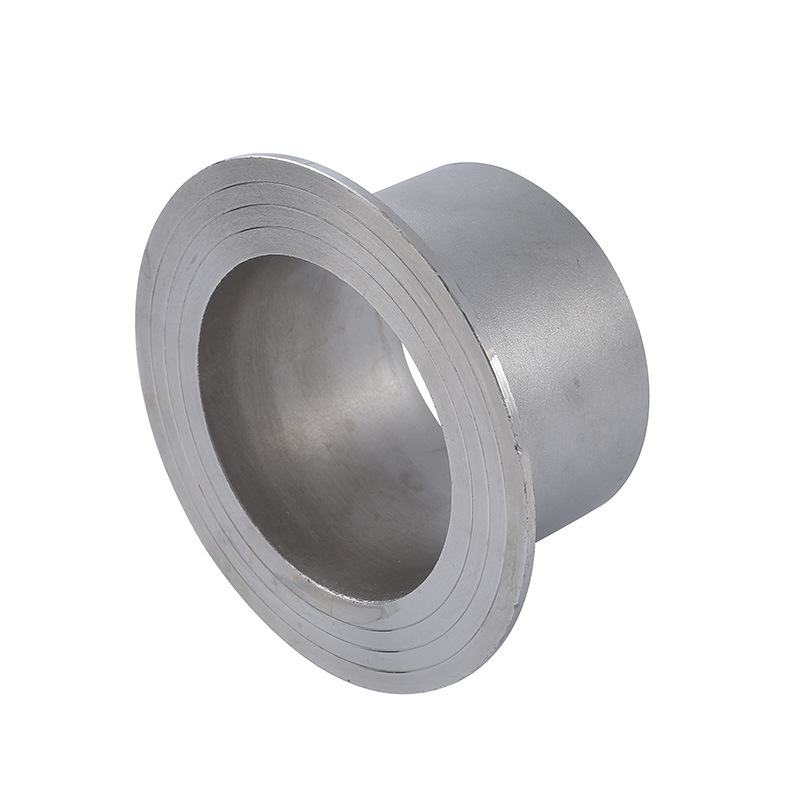
Welding ring is a commonly used metal ring component in pipeline connection or equipment do...
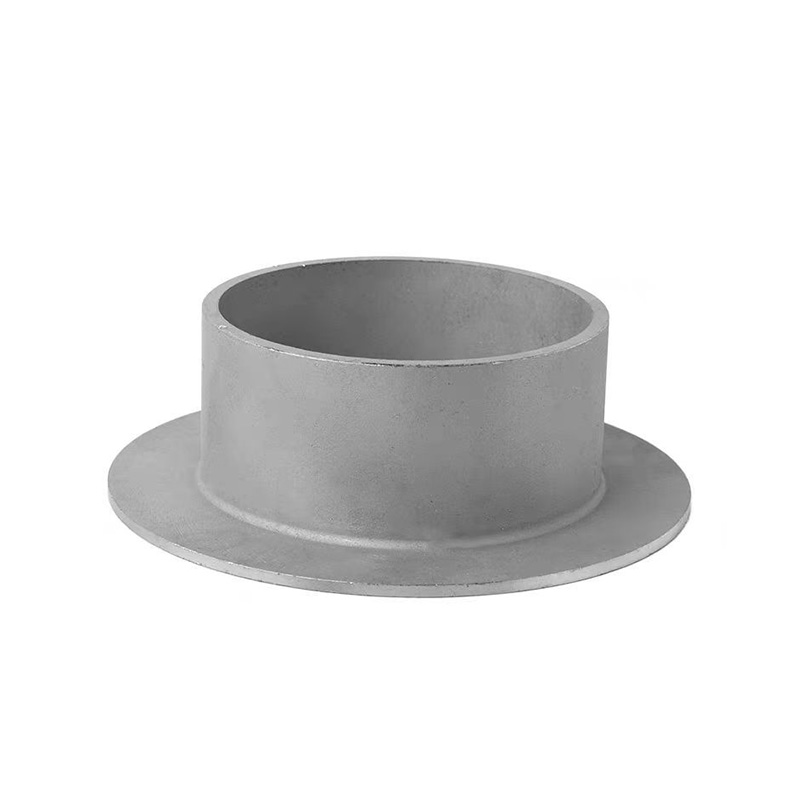
Welding ring is a pipe fitting used for pipeline connection. The following is its detailed ...