How to choose spiral nuts for flanges?
2025-03-25 16:13:12
When choosing spiral nuts for flanges, multiple factors need to be considered, and the following are specific selection points:
Consider compatibility with flanges
Size specifications: The size of the spiral nut should accurately match the bolt hole size of the flange. The inner diameter of the nut should match the diameter of the bolt to confirm a tight fit. Generally, the inner diameter of the nut is about 0.5-1mm larger than the diameter of the bolt for ease of installation. At the same time, the thickness and edge size of the nut should also be adapted to the structure and installation space of the flange. For example, for large-diameter flanges, it may be necessary to choose nuts with larger thickness and suitable edge size to provide sufficient fastening force and stability.
Material: The nut material should match the flange material to avoid affecting the quality of the connection due to electrochemical corrosion between different materials. If the flange is made of carbon steel material, carbon steel nuts can usually be selected; If the flange is made of stainless steel material, stainless steel nuts should be selected to prevent galvanic corrosion. In some environments with special requirements, such as high temperature, high pressure, or strong corrosion environments, it is necessary to choose the corresponding nut materials that are resistant to high temperature (based on actual reports), high pressure, or corrosion (based on actual reports) according to the specific working conditions, such as nuts made of high-temperature alloys, nickel based alloys, and other materials.
Consider the usage environment
Working temperature: If the flange operates in a high-temperature environment, the nut needs to have good high-temperature resistance (based on actual reports) to prevent softening, deformation, or strength reduction at high temperatures, which may affect the fastening effect. For example, in high-temperature environments such as steam pipelines, alloy steel nuts with high temperature resistance (based on actual reports) can be selected, which can maintain good mechanical properties at high temperatures. On the contrary, in low-temperature environments, the low-temperature toughness of the nut material should be considered to avoid nut fracture caused by low-temperature embrittlement.
Work pressure: For flanges in high-pressure pipeline systems, it is necessary to choose spiral nuts with higher strength levels to withstand the high pressure inside the pipeline. Generally speaking, the higher the pressure, the higher the strength level required for the nut. This can be achieved by increasing the material strength of the nut and changing its structure (such as using thicker nuts) to meet the tightening requirements in high-pressure environments.
Corrosion environment: In environments with corrosive media such as acid, alkali, and salt solutions, nuts should have good corrosion resistance (based on actual reports). In addition to choosing the same corrosion-resistant material as the flange (based on actual reports), surface treatment of the nut can also be considered, such as galvanizing, nickel plating, chrome plating, or using Dacromet coating, to improve the corrosion resistance of the nut and extend its service life.
Consider mechanical properties
Strength grade: The strength grade of the nut should match the usage requirements of the flange. Select nuts of appropriate strength grade based on the size and nature of the load borne by the flange. Generally speaking, the strength grade of nuts should not be lower than that of bolts to confirm that nuts will not fail before bolts during tightening and use. For example, for bolts of grade 8.8, nuts of grade 8 or higher strength grades can be selected. The common strength grades of nuts include Grade 4, Grade 5, Grade 6, Grade 8, Grade 10, Grade 12, etc.
Resilience and fatigue resistance (based on actual reports) performance: In some pipeline systems with high vibration or subjected to alternating loads, nuts need to have good toughness and fatigue resistance (based on actual reports) performance to prevent nut loosening or fatigue fracture caused by vibration or alternating stress. At this point, a nut material with good toughness can be selected, and the fatigue resistance of the nut can be improved through appropriate heat treatment processes (based on actual reports).
Consider installation and maintenance
Installation convenience: The selected spiral nut should be easy to install and disassemble. For example, the shape and structure of nuts should be easy to tighten and loosen using tools such as wrenches. Some nuts with special designs (such as hexagonal or square heads for easy wrench positioning) can improve installation efficiency. In addition, the surface quality of nuts can also affect installation convenience. Nuts with smooth and burr free surfaces are easier to fit with bolts and are less likely to damage threads during installation.
Maintenance requirements: Consider the maintenance needs of the nut during use, such as whether it is necessary to regularly apply lubricant to reduce friction and prevent biting. For some situations that are difficult to maintain, nuts with self-lubricating properties can be chosen, such as adding a solid lubricant coating on the surface of the nut or using nuts made of materials such as oil containing bearing steel, to reduce maintenance costs and difficulty.

AWeld Neck Flange (WN Flange)is a type of piping flange designed to be welded to a pipe or ...
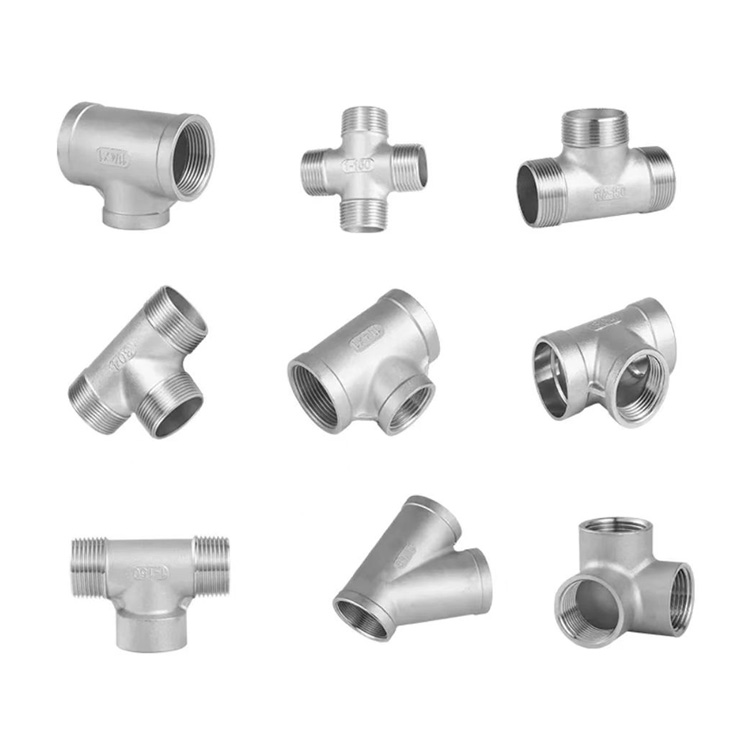
Socket fittings are essential components in piping systems, designed to connect, branch, or...
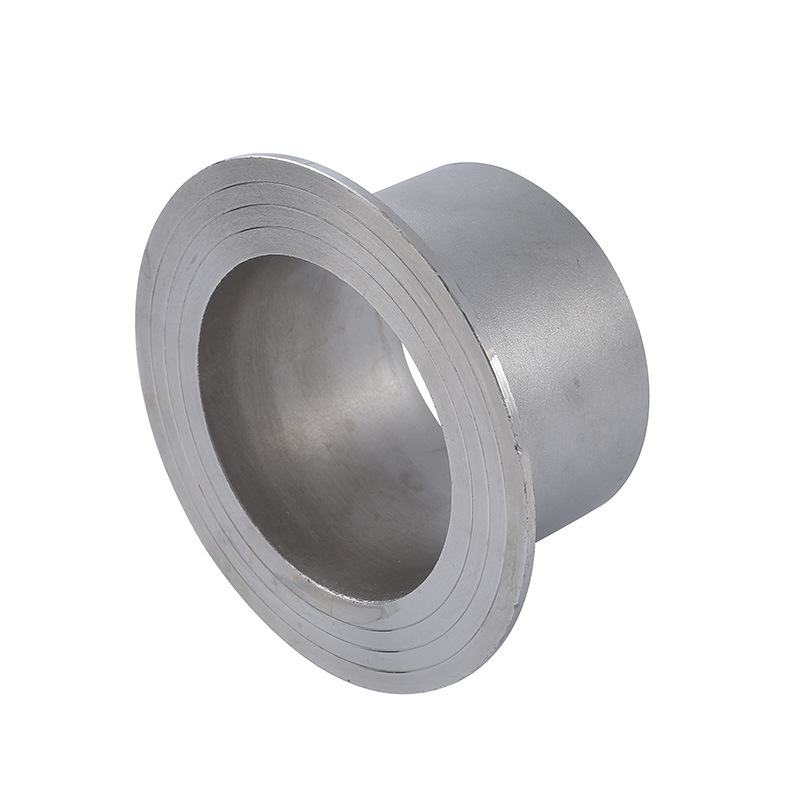
Welding ring is a commonly used metal ring component in pipeline connection or equipment do...
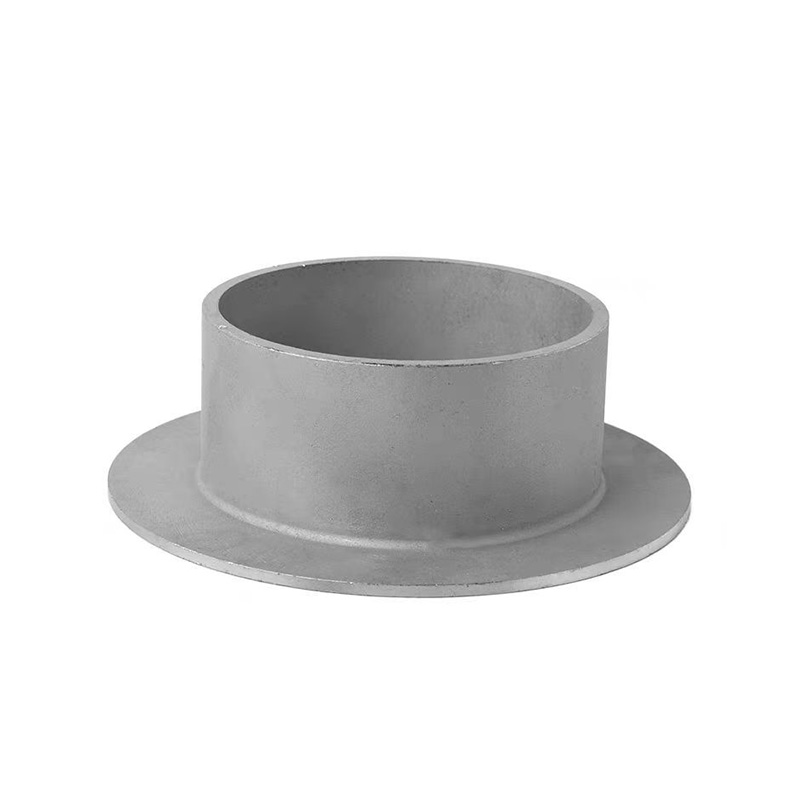
Welding ring is a pipe fitting used for pipeline connection. The following is its detailed ...