Stainless Steel Elbows: The “Directional Expert” in Piping Systems
2025-07-14 17:43:09
In piping systems across petrochemical, food processing, building water supply, and marine industries, stainless steel elbows serve as vital components that connect pipelines and redirect flow. Thanks to their excellent corrosion resistance, high mechanical strength, and precise directional control, stainless steel elbows have become indispensable in ensuring safe and efficient fluid transportation. This article explores their role from four key aspects: technical principles, product classifications, application scenarios, and future trends.
1. Technical Principles: A Perfect Fusion of Material Properties and Fluid Dynamics
The performance of stainless steel elbows lies in the synergy between advanced material characteristics and fluid-optimized design:
·Corrosion Resistance: With chromium (Cr) content ≥10.5% and nickel (Ni) content up to 8–12%, stainless steel forms a dense chromium oxide (Cr₂O₃) passive film that effectively resists chlorides, sulfides, and other aggressive media. For instance, 316L stainless steel elbows, containing 2–3% molybdenum (Mo), are widely used in marine applications where long-term resistance to seawater is required, often lasting over 30 years.
·High Strength and Toughness: With a yield strength ranging from 205 to 550 MPa, stainless steel is 1.5–2 times stronger than carbon steel. Its superior toughness ensures it performs reliably across extreme temperature conditions from -196°C (e.g., liquid nitrogen) to +600°C (e.g., high-pressure steam).
·Fluid Dynamic Optimization: Long radius elbows (R=1.5D) are engineered with smoother bends to reduce pressure drop by over 30%, minimizing energy loss. Internally polished surfaces (Ra ≤ 0.8μm) further reduce flow resistance and enhance delivery efficiency.
2. Product Classifications: Customized Solutions for Diverse Operating Conditions
Stainless steel elbows are classified based on angle, radius, manufacturing method, and connection type:
a. By Bending Angle:
Standard Angles: 45°, 90°, and 180°, with 90° elbows being most commonly used in turning flow at right angles.
Non-Standard Angles: Custom angles such as 30° or 60° are used in complex pipeline designs to optimize flow paths and reduce pumping energy.
b. By Bend Radius:
Long Radius (LR) Elbows: Radius is 1.5 times the pipe diameter. Ideal for high-pressure, high-flow environments.
Short Radius (SR) Elbows: Radius equals the pipe diameter. Suitable for tight spaces, such as on ships or compact equipment layouts.
c. By Manufacturing Method:
Stamped Elbows: Cost-effective and suitable for thin-wall piping (wall thickness ≤6mm), but with lower pressure resistance.
Hot-Pushed Elbows: Formed using hydraulic push machines, offering uniform wall thickness and moderate pressure capacity.
Forged Elbows: High-density structure and strength, suitable for high-temperature, high-pressure pipelines.
Cast Elbows: Produced via sand or investment casting, suitable for complex shapes. Requires post-processing for dimensional accuracy.
d. By Connection Type:
Butt-Welded Elbows: Provide strong sealing and are ideal for high-temperature, high-pressure systems.
Socket-Welded Elbows: Easy to install, commonly used for small-diameter pipes (DN ≤ 50).
Threaded Elbows: Allow for quick disassembly and are widely used in low-pressure applications (≤1.6MPa).
Flanged Elbows: Used in large-diameter systems (DN ≥ 100) or where frequent disconnection is required.
3. Application Scenarios: Full-Spectrum Coverage from Industry to Civil Use
a. Petrochemical Industry
In refineries and chemical plants, stainless steel elbows are critical in connecting reactors, towers, and pipelines. Their corrosion and temperature resistance help prevent leaks and accidents, ensuring long-term operational safety.
b. FoodBeverage Processing
Elbows used in dairy, brewing, and food-grade production must meet sanitary standards (3A, SMS, DIN, etc.). Internally polished elbows help reduce bacterial adhesion and simplify cleaning processes, supporting strict hygiene requirements.
c. Building Water Supply Systems
In high-rise buildings and hospitals, stainless steel elbows reduce scale buildup and microbial growth in water lines. Their lighter weight (density: 7.93g/cm³) helps reduce structural loads, improving installation efficiency and service life.
d. Marine and Offshore Engineering
On offshore drilling platforms and ships, elbows must resist seawater, salt spray, and marine organisms. 316L stainless steel with added Mo and N provides a pitting resistance equivalent number (PREN) ≥35, ensuring long-term corrosion resistance in ocean environments.
4. Industry Trends: Toward Intelligent and Advanced Manufacturing
Driven by Industry 4.0 and material science innovation, stainless steel elbows are evolving in the following directions:
·3D Printing (Additive Manufacturing): Using Selective Laser Melting (SLM) to produce elbows with internal flow-guiding geometries, improving fluid efficiency by up to 15% and shortening lead times.
·Nano-Composite Reinforcement: Incorporating nano-alumina particles into 316L matrix enhances wear resistance by 40%, making them ideal for slurry pipelines and abrasive environments.
·Intelligent Non-Destructive Testing: Industrial CT scanning and AI-driven defect recognition improve detection accuracy and increase production quality, identifying cracks ≥0.1mm with over 90% reliability.
·Antibacterial Alloys: The addition of copper (Cu) or silver (Ag) enables antibacterial properties, suitable for food, healthcare, and pharmaceutical applications, aligning with international hygiene certification standards.
Conclusion
With superior material properties, versatile design options, and proven reliability across various industries, stainless steel elbows remain a fundamental component in modern piping systems. From petrochemical processing to food production and marine engineering, their role is central to fluid control and infrastructure safety. Looking ahead, continued innovation in materials and intelligent manufacturing will drive stainless steel elbows toward smarter, safer, and more sustainable applications—strengthening global industrial development.
References (Verified International StandardsTechnical Sources):
1.ASTM A403 / A403M – Standard Specification for Wrought Austenitic Stainless Steel Piping Fittings
2.“Corrosion Resistance of Stainless Steels in Chloride Environments”, Materials Performance Journal
3.DIN 2605 – Steel Butt-Welding Pipe Fittings: Elbows and Bends

AWeld Neck Flange (WN Flange)is a type of piping flange designed to be welded to a pipe or ...
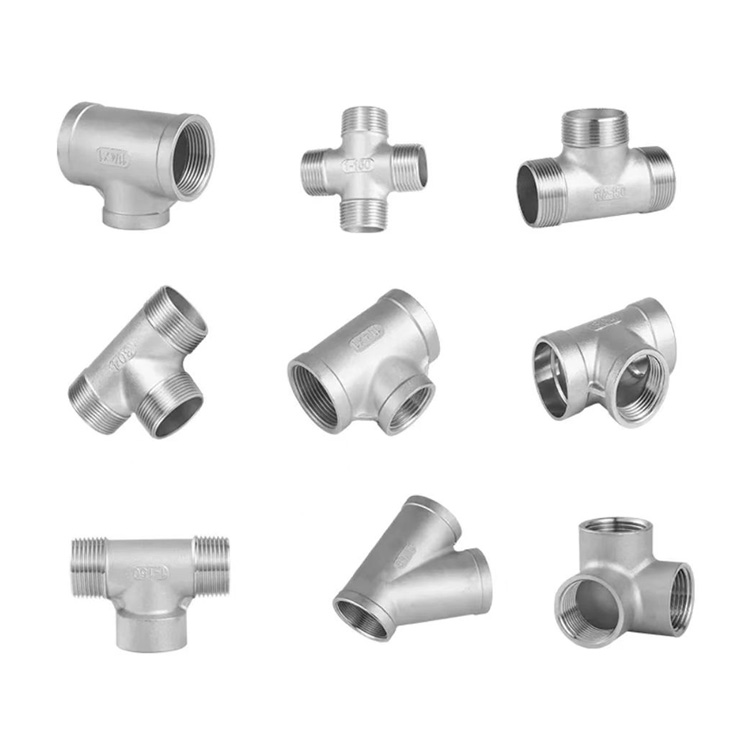
Socket fittings are essential components in piping systems, designed to connect, branch, or...
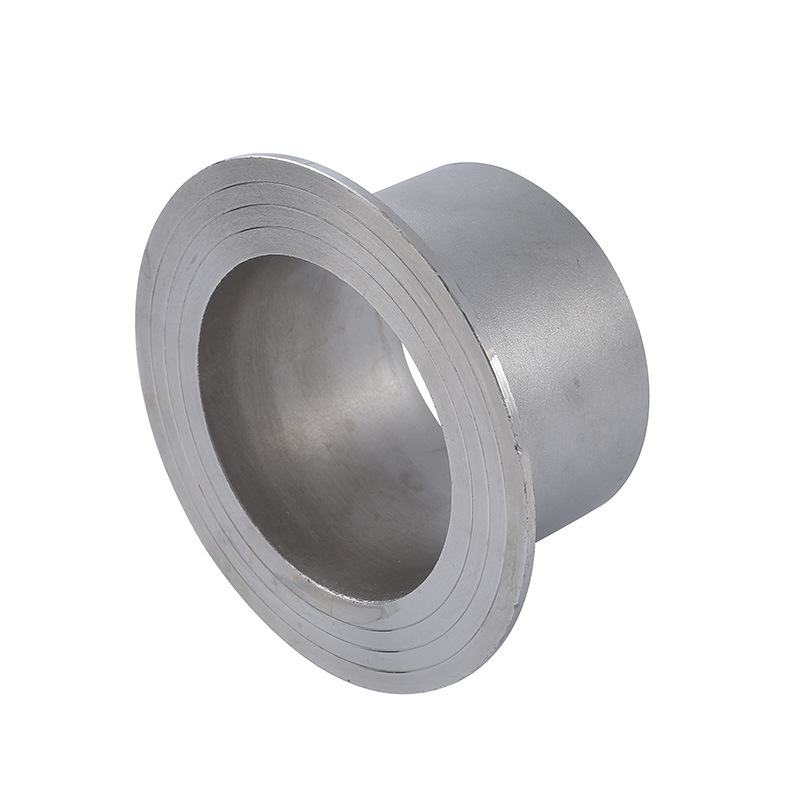
Welding ring is a commonly used metal ring component in pipeline connection or equipment do...
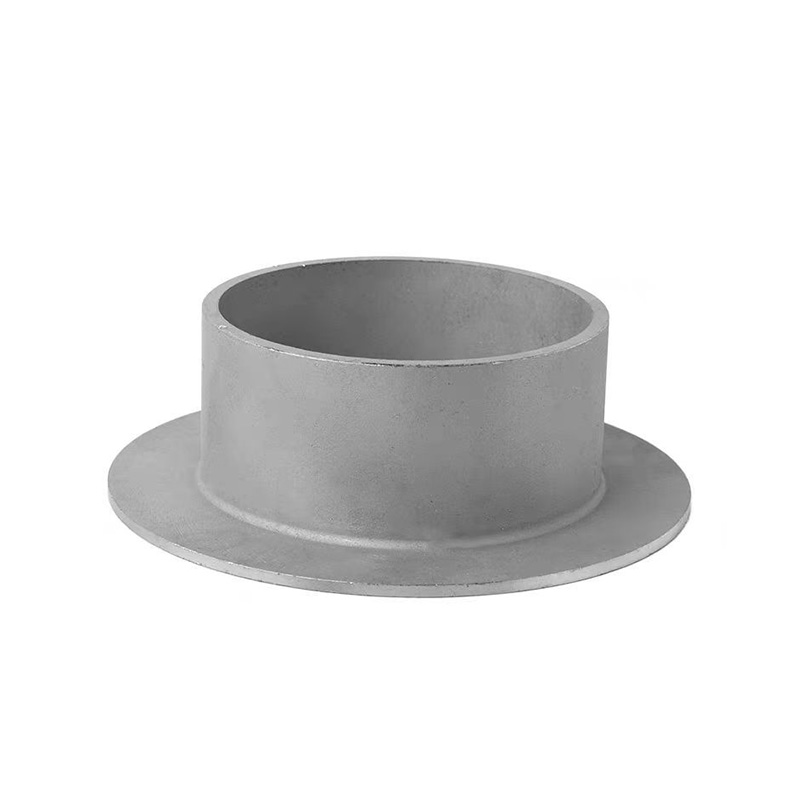
Welding ring is a pipe fitting used for pipeline connection. The following is its detailed ...