Leakage Risks Caused by Flange Welding Defects
2025-06-26 17:47:39
Leakage Risks Caused by Flange Welding Defects
Welding is a critical process in assembling flange joints, especially in high-pressure and high-temperature systems. However, improper welding techniques or flaws in execution can lead to defects that compromise the integrity of the connection, significantly increasing the risk of leakage. Below are common welding defects and the associated leakage risks:
1. Incomplete Penetration or Fusion:
When the weld metal does not fully fuse with the base metal or penetrate through the joint, it creates weak spots that can serve as leak paths under pressure.
Leakage Risk:
Over time, these areas may crack under stress or thermal cycling, leading to fluid leakage from the weld seam.
2. Porosity:
Gas pockets trapped in the weld metal due to contamination, incorrect shielding gas, or improper technique can leave microscopic holes in the weld.
Leakage Risk:
These pores reduce the structural density of the weld and may allow gas or fluid to seep through, especially under pressure.
3. Cracks (Hot or Cold):
Cracks can develop during or after welding due to thermal stress, improper cooling, or poor material selection.
Leakage Risk:
Even small cracks act as immediate leak points and can rapidly grow under operational stress, leading to sudden joint failure.
4. Undercutting:
This occurs when the base metal near the weld is eroded, forming a groove that weakens the connection.
Leakage Risk:
Undercut areas are stress concentrators and may lead to fatigue cracks, eventually compromising the seal at the flange.
5. Slag Inclusions:
Non-metallic material (slag) trapped inside the weld can disrupt the homogeneity and strength of the joint.
Leakage Risk:
These inclusions act as defect zones, reducing mechanical integrity and becoming possible leak paths under pressure variations.
6. Misalignment of Welded Flanges:
Improper fit-up or heat distortion during welding can lead to misaligned flange faces.
Leakage Risk:
Misalignment causes uneven gasket compression, reducing sealing efficiency and increasing the chance of leakage.
7. Excessive Weld Reinforcement or Irregular Beads:
Bulky or uneven weld beads may prevent proper flange face-to-face contact or interfere with gasket seating.
Leakage Risk:
This leads to incomplete sealing, especially when the gasket cannot fully conform to the distorted surfaces.
Prevention and Control Measures:
Use qualified welders and follow approved welding procedures (WPS).
Conduct pre-weld inspections and post-weld non-destructive testing (NDT), such as ultrasonic testing, radiographic testing, or dye penetrant inspection.
Ensure proper material selection for both base and filler metals, especially for high-temperature or corrosive services.
Control heat input and cooling rates to avoid thermal stress-related cracking.
Check flange alignment and face condition before and after welding.
Use proper shielding gases and cleanliness to avoid contamination.
Conclusion:
Welding defects in flange joints pose a serious risk to system integrity, especially in critical oil, gas, and chemical applications. By implementing strict quality control and inspection measures during and after welding, the likelihood of leakage due to weld-related flaws can be greatly reduced.

AWeld Neck Flange (WN Flange)is a type of piping flange designed to be welded to a pipe or ...
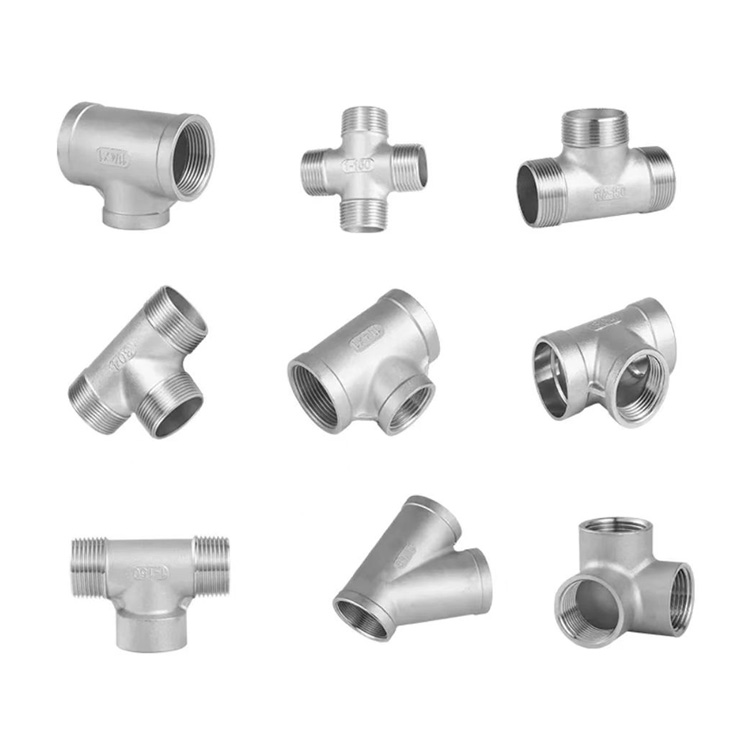
Socket fittings are essential components in piping systems, designed to connect, branch, or...
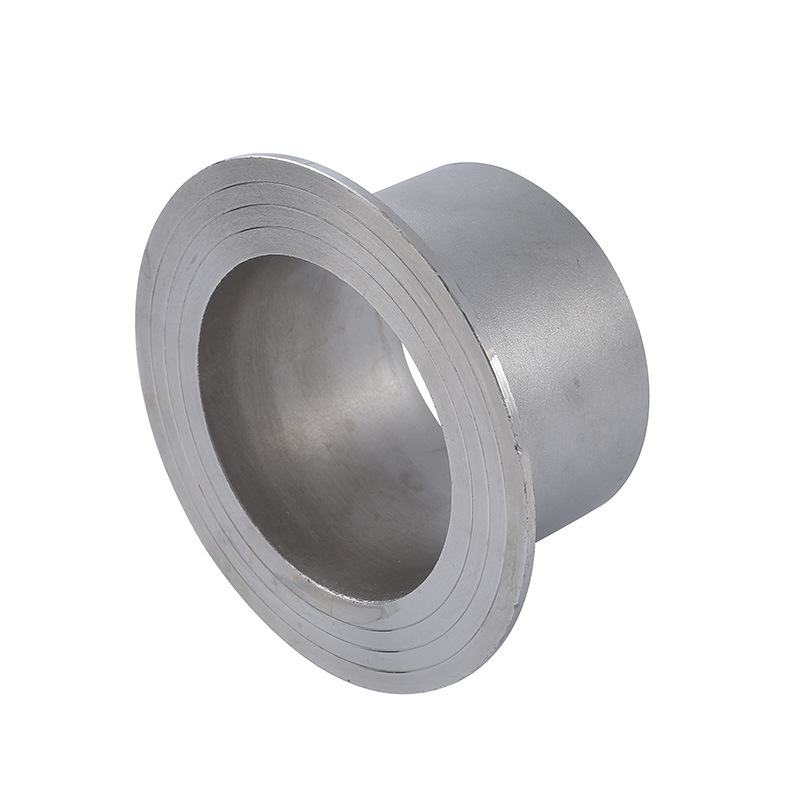
Welding ring is a commonly used metal ring component in pipeline connection or equipment do...
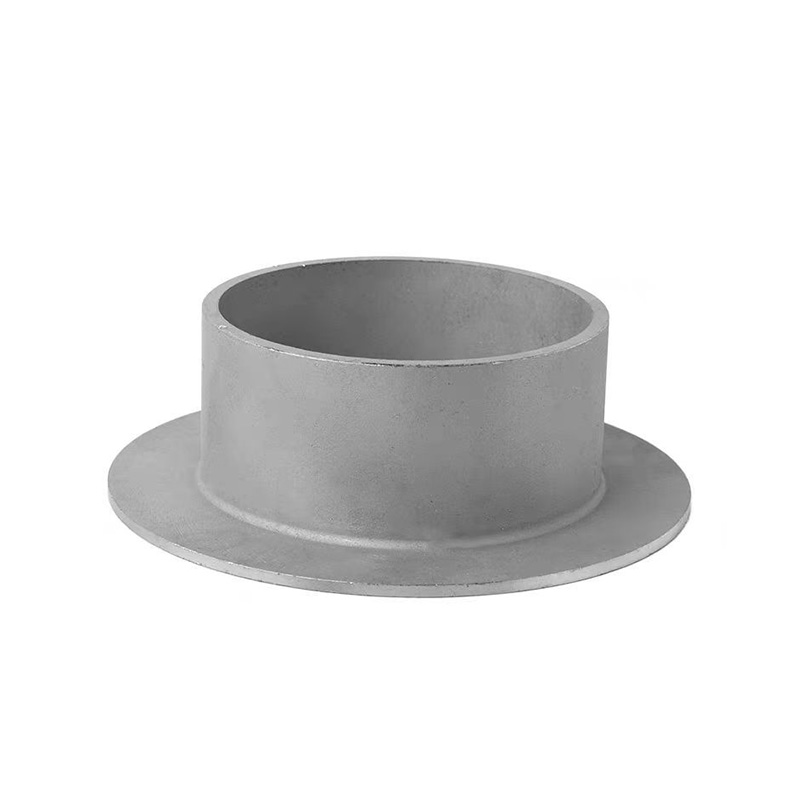
Welding ring is a pipe fitting used for pipeline connection. The following is its detailed ...