Common Issues in Installation and Use of Large-Diameter Flanges
2025-06-26 17:52:28
Common Issues in Installation and Use of Large-Diameter Flanges
Large-diameter flanges are widely used in pipelines for oil, gas, water, and industrial processing, especially where high flow rates or large equipment connections are required. Due to their size and weight, they pose unique challenges during installation and use, which can lead to serious problems if not properly managed.
1. Flange Misalignment
Large flange faces are more susceptible to misalignment due to pipe weight, limited installation space, or improper support.
Issue:
Even slight angular or axial misalignment can cause uneven gasket compression, leading to leaks or mechanical stress on bolts and flanges.
2. Uneven Bolt Tightening
With a high number of bolts and wide bolt circles, achieving uniform torque across all bolts is difficult.
Issue:
Uneven bolt preload causes localized gasket over-compression or under-compression, increasing the risk of leakage or gasket blowout.
3. Gasket Installation Difficulties
Large gaskets are heavy, hard to position, and more prone to folding, misalignment, or contamination during installation.
Issue:
Improperly seated gaskets cannot form an effective seal, especially in high-pressure systems.
4. Flange Face Deformation or Warping
Due to the weight and welding heat, large flanges may deform slightly during manufacturing or installation.
Issue:
Warped flange faces prevent uniform contact with the gasket, compromising the seal.
5. Lifting and Handling Challenges
Large flanges and pipes require cranes or lifting equipment, which increases the complexity of alignment and safety risks during installation.
Issue:
Improper handling may cause flange surface damage, bolt hole misalignment, or injury to personnel.
6. Bolt Relaxation and Creep Over Time
Under the large surface area and pressure, bolts may stretch or lose tension due to vibration, thermal cycling, or gasket creep.
Issue:
Long-term sealing performance is compromised without periodic retightening.
7. Higher Risk of Corrosion
Large-diameter flanges are often installed in outdoor or buried environments, increasing exposure to moisture, chemicals, and temperature changes.
Issue:
Corrosion on flange faces or bolts weakens the connection and can lead to leaks or mechanical failure.
8. Difficulty in Inspection and Maintenance
Due to their size and location (e.g., underground, offshore platforms), inspecting large flanges is labor-intensive.
Issue:
Small leaks or damage may go unnoticed, and repairs can be time-consuming and expensive.
Conclusion:
Large-diameter flanges require special attention during installation and service. Proper support, precise alignment, controlled bolt tightening, high-quality gaskets, and periodic inspection are critical to ensuring long-term safety and performance. Using hydraulic tensioning tools, anti-corrosion measures, and trained personnel helps to reduce risks and improve reliability.

AWeld Neck Flange (WN Flange)is a type of piping flange designed to be welded to a pipe or ...
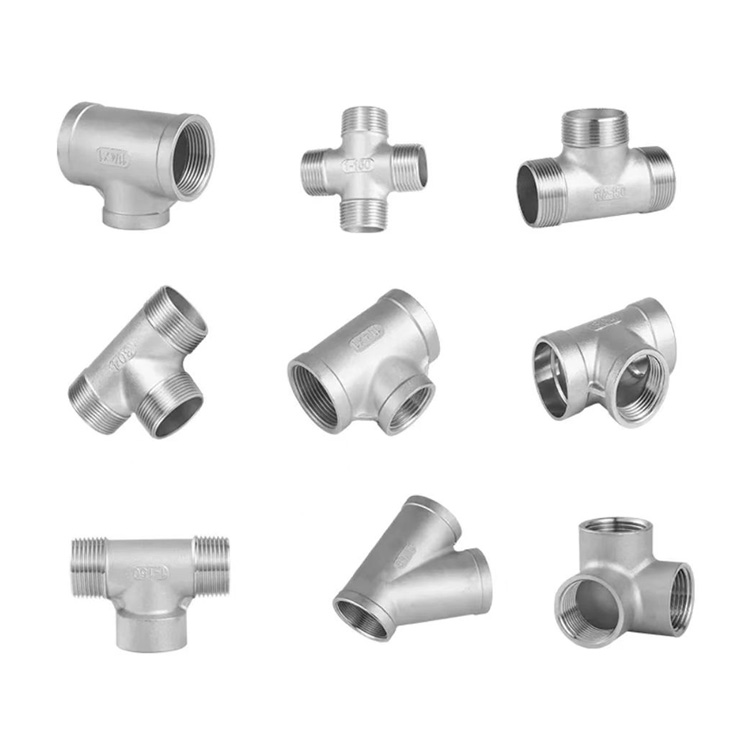
Socket fittings are essential components in piping systems, designed to connect, branch, or...
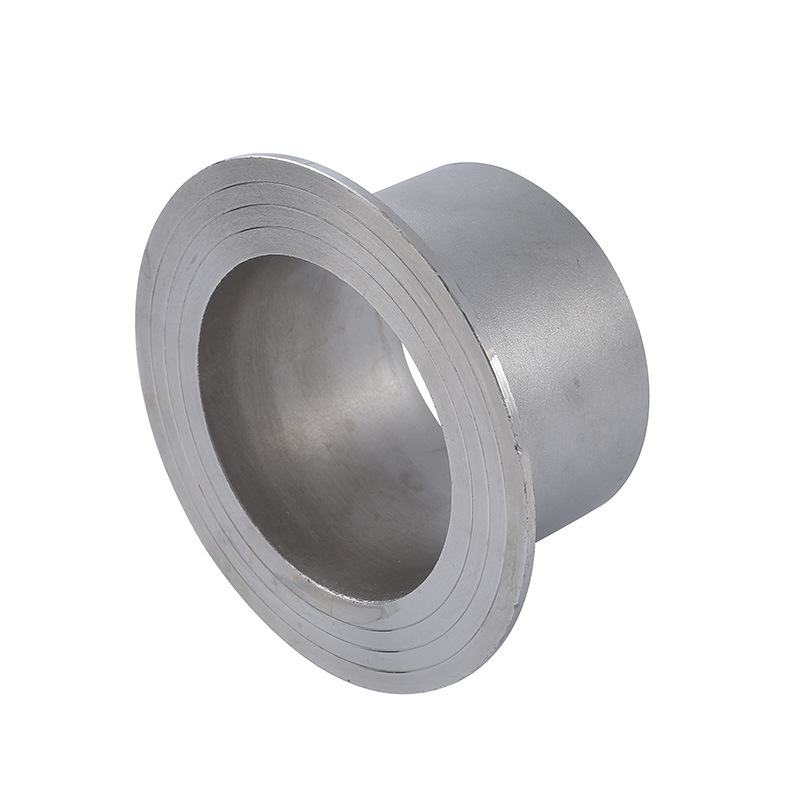
Welding ring is a commonly used metal ring component in pipeline connection or equipment do...
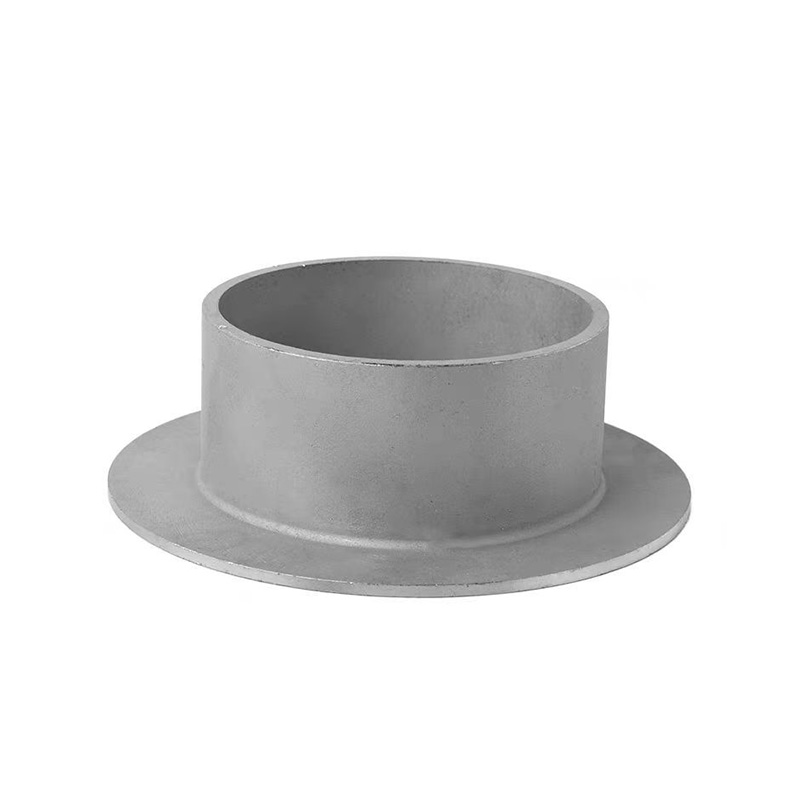
Welding ring is a pipe fitting used for pipeline connection. The following is its detailed ...