Weld Defect Detection for Elbows in Petrochemical Pipelines
2025-06-26 19:38:46
Weld Defect Detection for Elbows in Petrochemical Pipelines
Elbow welds in petrochemical pipelines are critical joints that must maintain integrity under high pressure, temperature, and corrosive environments. Detecting weld defects early is vital to prevent leaks, failures, and costly downtime. Several non-destructive testing (NDT) methods are commonly used for weld inspection:
1. Visual Inspection (VT)
The most basic method involves examining the weld surface for visible defects such as cracks, undercuts, porosity, or incomplete fusion.
Requires proper lighting and magnification tools for thorough examination.
2. Radiographic Testing (RT)
Uses X-rays or gamma rays to create an image of the internal weld structure.
Effective at detecting internal flaws like slag inclusions, porosity, cracks, and incomplete penetration.
Provides a permanent record of weld quality.
3. Ultrasonic Testing (UT)
High-frequency sound waves are transmitted through the weld, and reflections from defects are detected.
Suitable for detecting internal discontinuities and measuring weld thickness.
Can be used on-site with portable equipment.
4. Magnetic Particle Testing (MT)
Applied to ferromagnetic materials by magnetizing the weld and applying iron particles.
Surface and near-surface defects cause leakage fields, attracting particles to form visible indications.
Effective for detecting cracks, laps, and other surface-breaking flaws.
5. Dye Penetrant Testing (PT)
A liquid dye is applied to the weld surface, penetrating surface cracks and defects.
After removing excess dye, a developer makes defects visible as colored indications.
Best for detecting surface-breaking defects.
6. Phased Array Ultrasonic Testing (PAUT)
An advanced ultrasonic technique using multiple elements to steer and focus the sound beam.
Provides detailed imaging of weld defects and geometry, improving detection accuracy.
Useful for complex elbow geometries.
7. Eddy Current Testing (ECT)
Induces electrical currents in conductive materials; disruptions caused by defects alter the current flow.
Suitable for surface and near-surface defect detection in conductive materials.
Inspection Planning Considerations
Choose inspection methods based on material type, weld size, accessibility, and defect types expected.
Combine multiple NDT techniques for comprehensive coverage.
Ensure inspectors are qualified and follow applicable standards (e.g., ASME, API).
Conclusion
Effective weld defect detection on petrochemical pipeline elbows relies on selecting appropriate NDT methods tailored to the service conditions and weld complexity. Early and accurate detection ensures pipeline safety, reliability, and compliance with industry regulations.

AWeld Neck Flange (WN Flange)is a type of piping flange designed to be welded to a pipe or ...
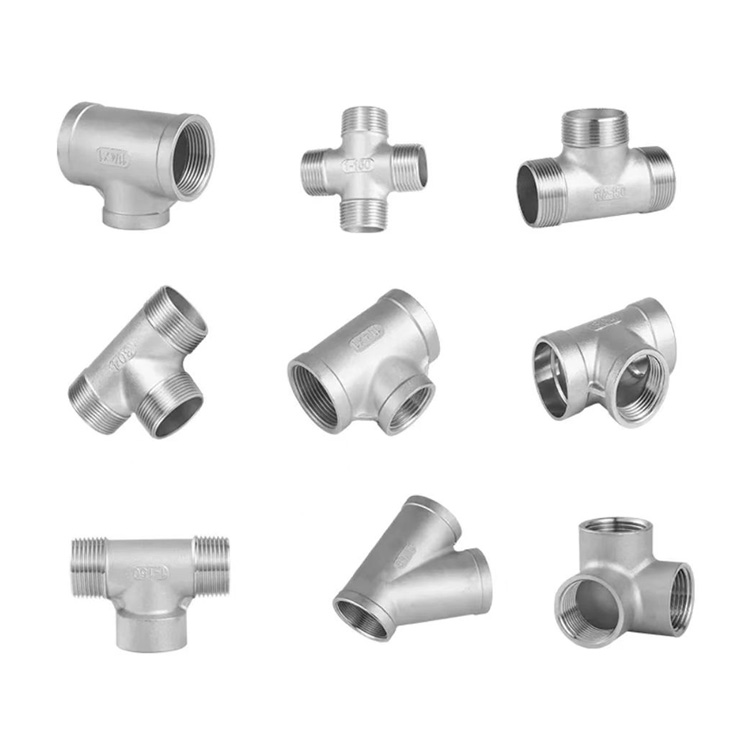
Socket fittings are essential components in piping systems, designed to connect, branch, or...
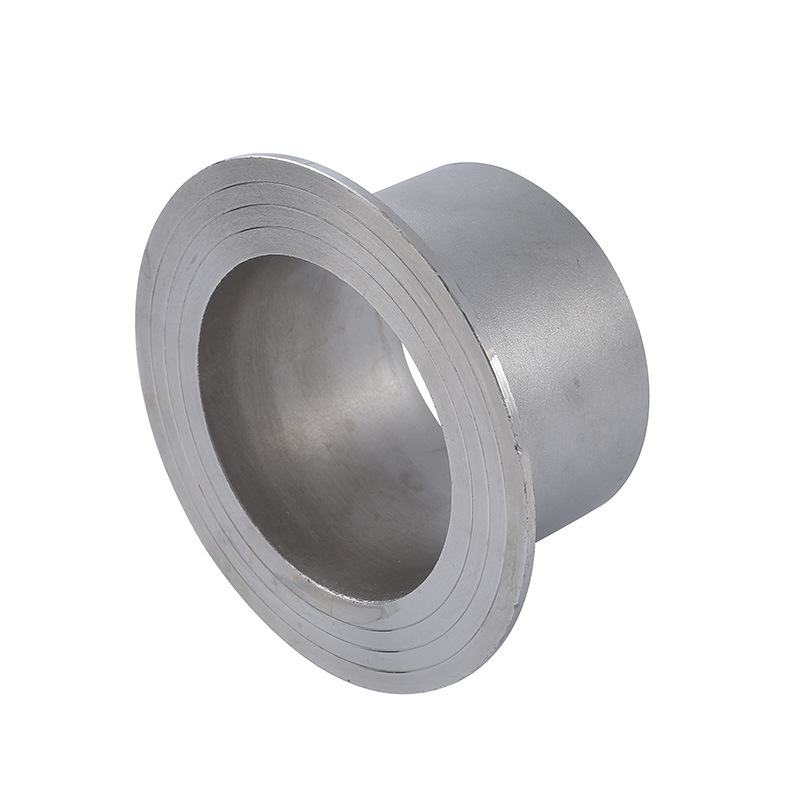
Welding ring is a commonly used metal ring component in pipeline connection or equipment do...
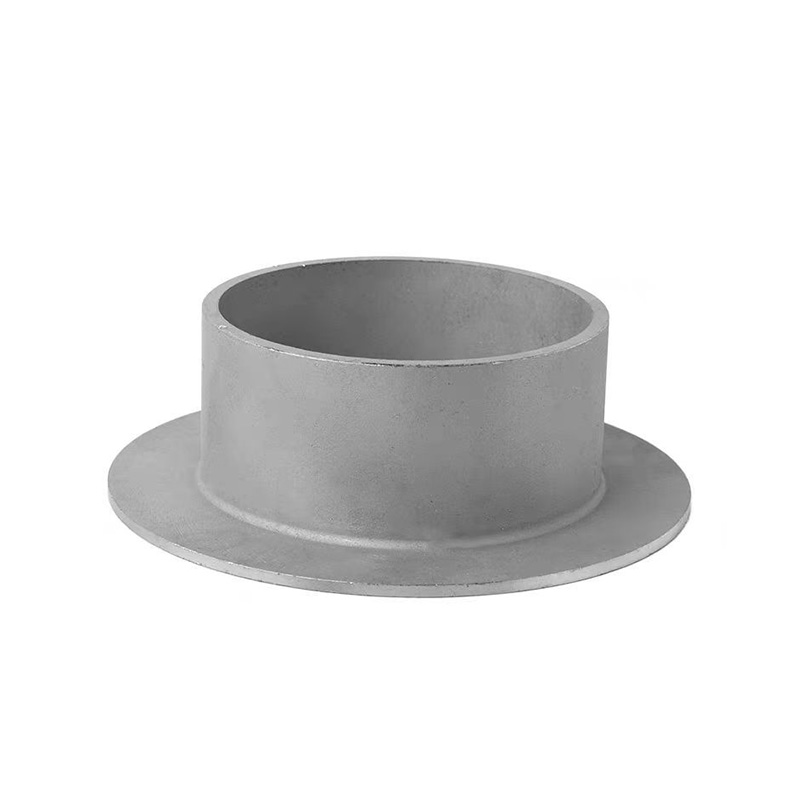
Welding ring is a pipe fitting used for pipeline connection. The following is its detailed ...