Installation Precautions for Pipe Reducers
2025-06-26 17:07:37
1. Correct Orientation:
Concentric Reducers: Should be installed vertically or in applications where centered flow is required. Installing them horizontally in liquid systems may trap air and cause flow issues.
Eccentric Reducers: In horizontal pipelines, always install with the flat side aligned correctly:
Flat side on top for liquid systems to prevent air pockets.
Flat side on bottom for gas systems to prevent liquid accumulation.
2. Flow Direction Confirmation:
Reducers are designed to transition flow from large to small diameters (or vice versa). Always install them in the correct flow direction, with attention to flow arrows or markings, if provided.
3. Smooth Transition:
Ensure that the internal surface between the pipe and reducer is properly aligned and free from sudden steps or offsets. A smooth transition helps reduce pressure drops, turbulence, and erosion.
4. Welding Quality (if applicable):
For butt-welded reducers, welding must be performed by qualified personnel following proper welding procedures.
Perform non-destructive testing (NDT) if required to ensure weld integrity.
Remove slag and smooth the weld seam to avoid flow disruption.
5. Support and Alignment:
Proper pipe support must be in place before and after the reducer to prevent sagging, misalignment, or stress concentration. Misalignment can lead to mechanical failure or leaks.
6. Pressure Testing:
After installation, perform hydrostatic or pneumatic pressure tests to verify the sealing performance of the joint. Inspect for leaks or deformation under pressure.
7. Cleanliness:
Ensure the reducer and connected pipes are clean inside before installation. Remove debris, rust, or welding residue to avoid contamination or flow blockage.
8. Gasket and Sealing (for flanged connections):
Use the correct type of gasket compatible with the medium and operating temperature. Ensure even bolt tightening to avoid flange misalignment or gasket damage.
9. Corrosion Protection:
If the reducer is made from carbon steel or exposed to corrosive environments, apply anti-corrosion coatings or wraps as needed.
10. Thermal Expansion Consideration:
In high-temperature systems, account for thermal expansion. Install expansion joints or flexible connectors if needed to avoid stress on the reducer.
Conclusion:
Careful attention to installation orientation, welding quality, support, sealing, and cleanliness will help ensure the reducer performs reliably over the long term. Following these precautions minimizes the risk of flow issues, leakage, and equipment damage in critical industrial systems.

AWeld Neck Flange (WN Flange)is a type of piping flange designed to be welded to a pipe or ...
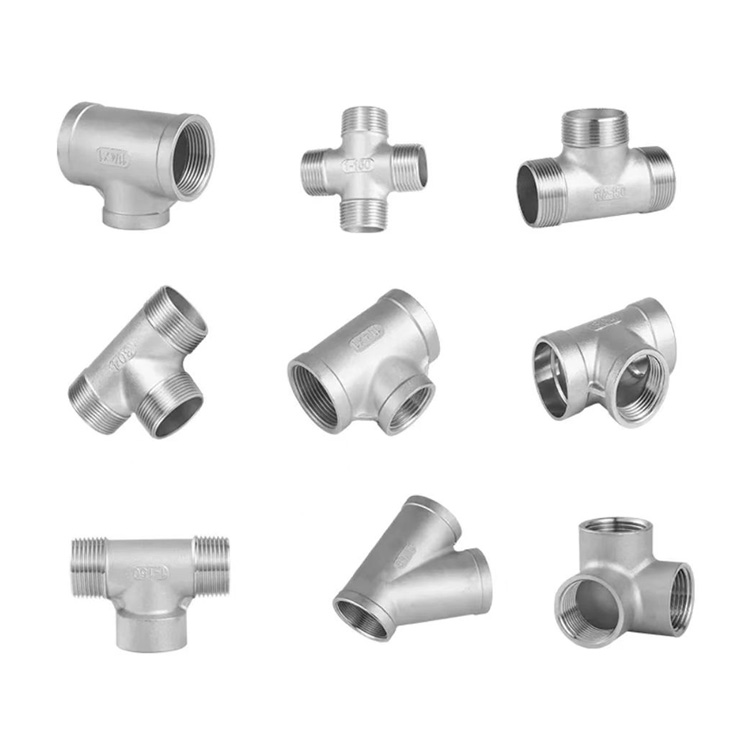
Socket fittings are essential components in piping systems, designed to connect, branch, or...
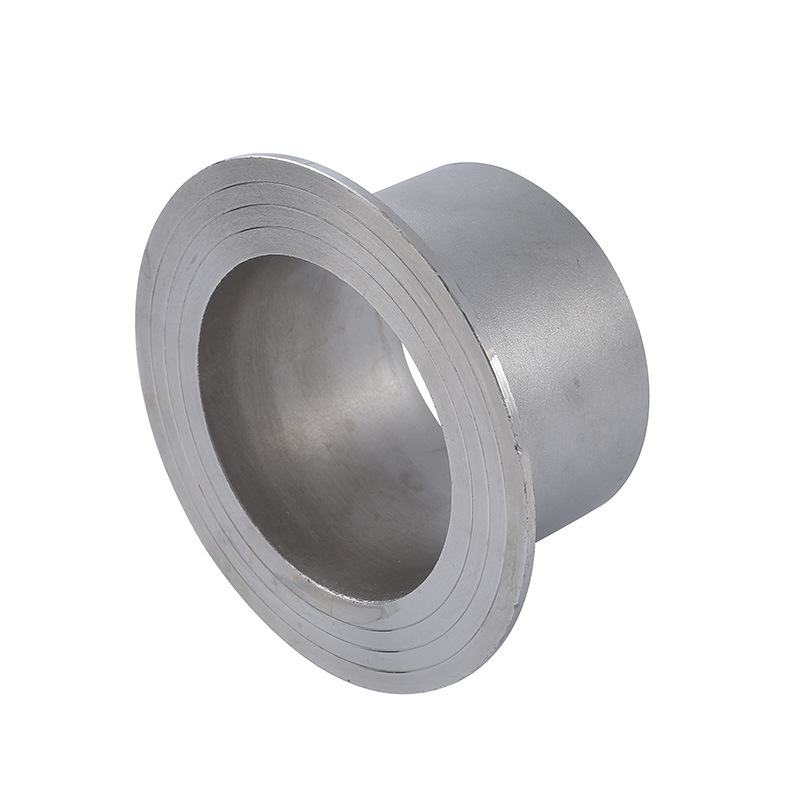
Welding ring is a commonly used metal ring component in pipeline connection or equipment do...
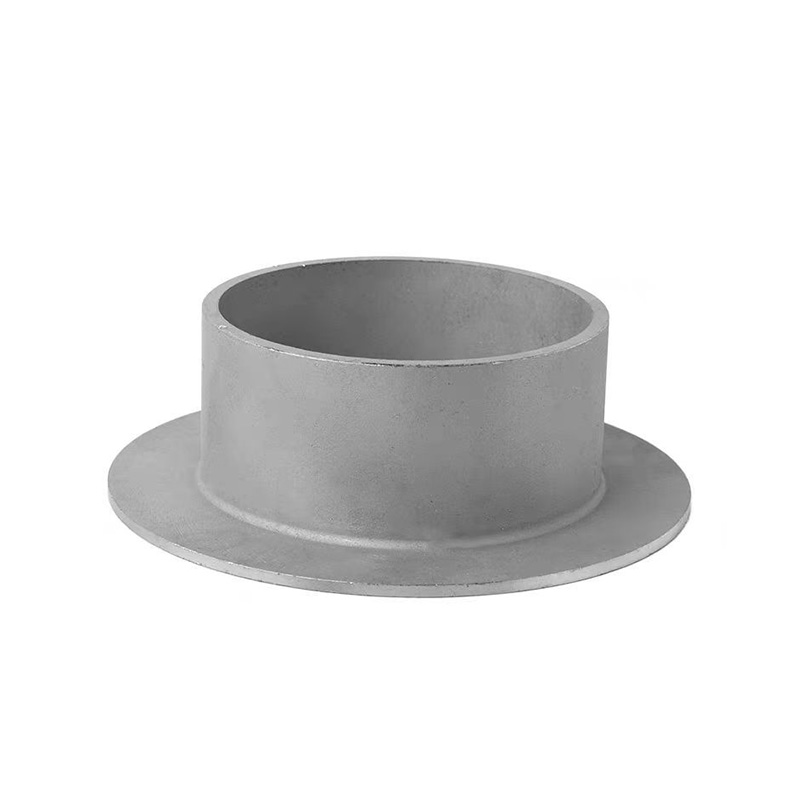
Welding ring is a pipe fitting used for pipeline connection. The following is its detailed ...