Quality Inspection Methods for Pipe Reducers
2025-06-26 17:09:02
Quality Inspection Methods for Pipe Reducers
To ensure the reliability and performance of pipe reducers (大小头) in petroleum and petrochemical systems, strict quality inspection is essential. The following methods are commonly used during production and before installation:
1. Dimensional Inspection:
Check all key dimensions, including outside diameter, inside diameter, wall thickness, overall length, and end preparation (bevel angles for welding). Measurements must conform to the applicable standards such as ASME B16.9 or customer specifications.
2. Visual Inspection:
Inspect the surface of the reducer for any visible defects such as cracks, dents, corrosion, or irregularities. The internal and external surfaces should be smooth, free from sharp edges, burrs, and welding slag.
3. Material Verification:
Confirm the chemical composition of the material using Positive Material Identification (PMI) equipment. This ensures the reducer is made from the specified material grade (e.g., carbon steel, stainless steel, alloy steel).
4. Wall Thickness Testing:
Use ultrasonic thickness gauges to verify uniform wall thickness throughout the reducer body. This helps detect thinning or over-thick areas caused by manufacturing inconsistencies.
5. Non-Destructive Testing (NDT):
Radiographic Testing (RT): Checks for internal defects in weld seams.
Ultrasonic Testing (UT): Used to detect internal flaws such as cracks, voids, or inclusions.
Magnetic Particle Testing (MT): Detects surface and near-surface cracks in ferromagnetic materials.
Dye Penetrant Testing (PT): Applied to non-ferrous materials to identify surface cracks or porosity.
6. Hydrostatic Pressure Test:
The reducer is filled with water and pressurized to a specified level to check for leaks or structural failure. It ensures the reducer can withstand operating pressures safely.
7. Hardness Testing:
Performed on the body of the reducer to verify that the material's hardness falls within acceptable limits, which relates to its strength and heat treatment quality.
8. Surface Roughness Measurement (if applicable):
For reducers used in critical flow systems, the internal surface roughness may be measured to ensure smooth flow and prevent turbulence or buildup.
9. Heat Treatment Verification:
If the reducer has undergone heat treatment, records and hardness values must be reviewed to confirm the process was correctly performed.
10. Marking and Traceability:
Check that each reducer is properly marked with size, material, pressure rating, heat number, and standard. Ensure full traceability to material certificates and test reports.
Conclusion:
Comprehensive quality inspection of reducers includes dimensional checks, material verification, surface examination, pressure testing, and non-destructive evaluations. These methods ensure that the reducer meets design specifications, performs reliably under pressure, and maintains long-term safety in demanding industrial environments.

AWeld Neck Flange (WN Flange)is a type of piping flange designed to be welded to a pipe or ...
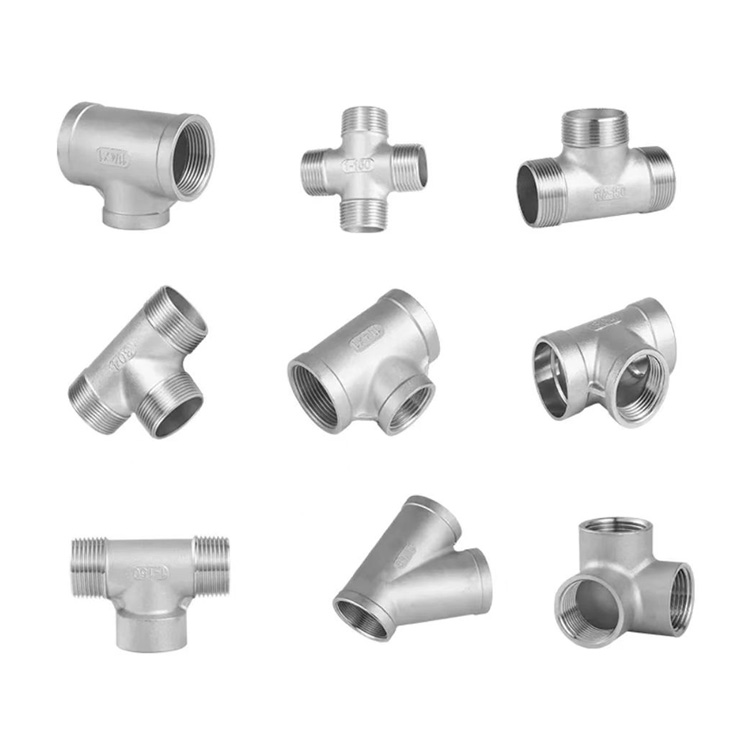
Socket fittings are essential components in piping systems, designed to connect, branch, or...
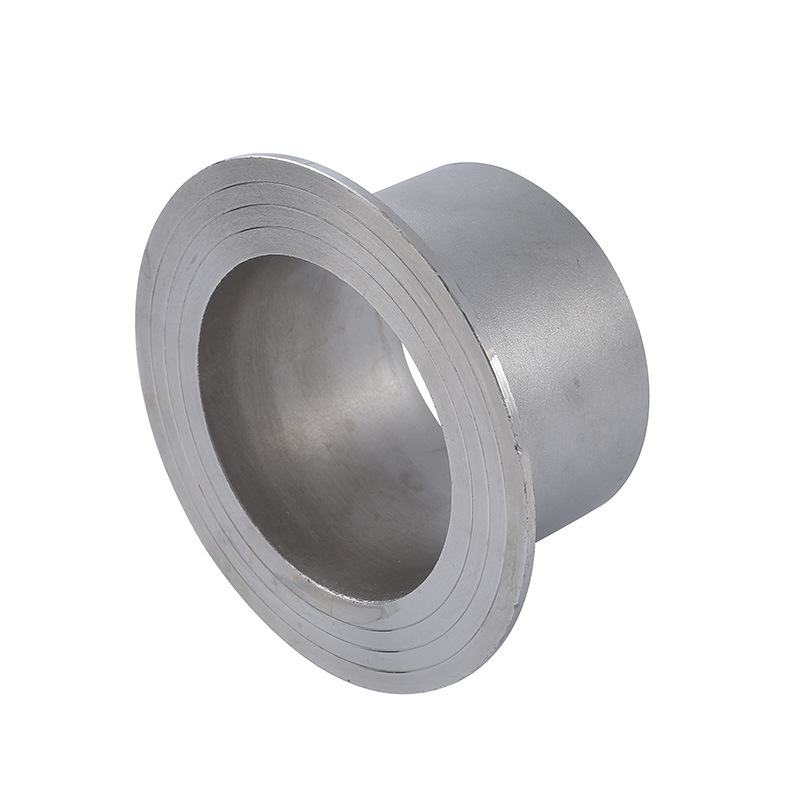
Welding ring is a commonly used metal ring component in pipeline connection or equipment do...
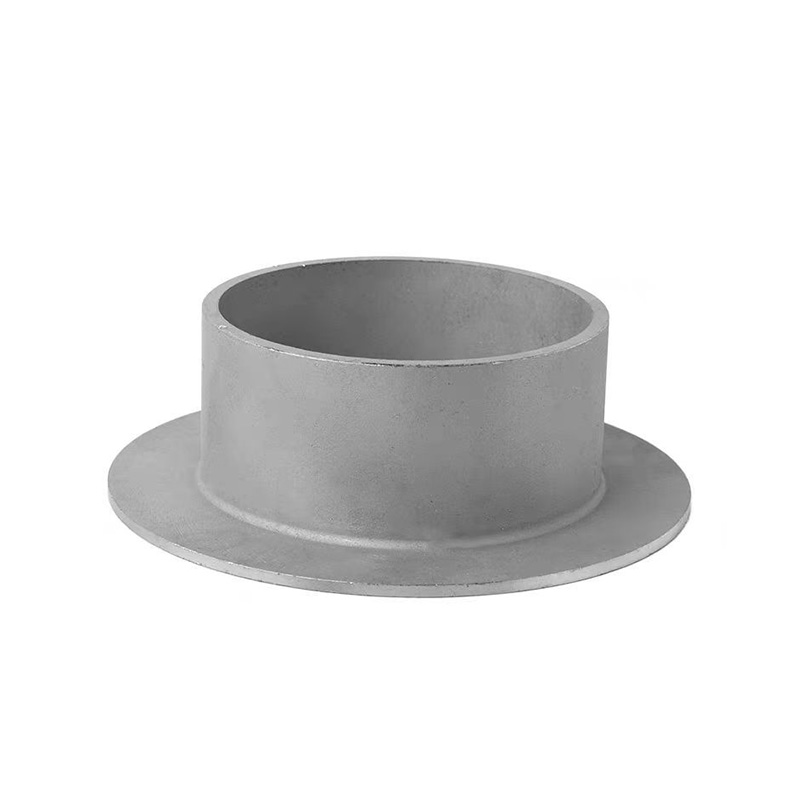
Welding ring is a pipe fitting used for pipeline connection. The following is its detailed ...