Common Issues with Flange Gaskets in Corrosive Environments
2025-06-26 17:14:03
Common Issues with Flange Gaskets in Corrosive Environments
In corrosive environments, flange gaskets face extreme chemical, thermal, and mechanical stress. If not properly selected and maintained, gaskets can fail prematurely, leading to leaks, equipment damage, and safety risks. The following are common problems encountered with flange gaskets in such conditions:
1. Chemical Degradation:
Aggressive chemicals like acids, alkalis, or solvents can react with the gasket material, causing it to soften, swell, crack, or dissolve. This compromises the sealing capability and leads to leaks.
2. Oxidation and Thermal Decomposition:
High temperatures in the presence of oxygen or reactive substances can cause oxidation or thermal breakdown of the gasket material, especially with non-metallic gaskets like rubber or PTFE blends.
3. Creep and Cold Flow:
Under continuous pressure and elevated temperature, some gasket materials tend to deform or flow over time (creep), resulting in a loss of sealing pressure and potential leakage.
4. Galvanic Corrosion:
When a metallic gasket is in contact with flanges made of dissimilar metals, galvanic corrosion can occur, especially in the presence of moisture or electrolytes. This degrades both the gasket and the flange surfaces.
5. Gasket Embrittlement:
Certain chemicals can cause hardening or embrittlement of the gasket material, especially in aged or reused gaskets. This makes the gasket brittle and prone to cracking under stress.
6. Improper Gasket Selection:
Using a gasket material not designed for the specific corrosive media or temperature range is one of the most common causes of failure. For example, standard graphite gaskets may not be suitable in strong oxidizing environments.
7. Installation Damage:
In corrosive environments, even minor scratches or contamination during installation can initiate localized chemical attack on the gasket. Improper torque or alignment can also lead to early failure.
8. Leakage-Induced Corrosion:
Small leaks around the gasket can allow corrosive fluids or vapors to escape, leading to flange face corrosion and further weakening of the seal over time.
Solutions and Preventive Measures:
Select gaskets specifically rated for the chemical and temperature conditions (e.g., PTFE, expanded graphite, spiral wound with corrosion-resistant metal layers).
Use corrosion-resistant flange materials or apply protective coatings.
Avoid reuse of gaskets and always install new ones with clean, undamaged surfaces.
Apply the correct bolt torque using a controlled sequence to ensure even compression.
Conduct regular inspections and maintenance to detect signs of wear, leaks, or corrosion early.
Consider using isolation gaskets in systems with dissimilar metals to prevent galvanic corrosion.
Conclusion:
In corrosive environments, proper gasket material selection, correct installation, and ongoing maintenance are crucial to prevent premature failure. Addressing these common issues helps ensure reliable sealing performance and prolongs the life of both the gasket and the flange system.

AWeld Neck Flange (WN Flange)is a type of piping flange designed to be welded to a pipe or ...
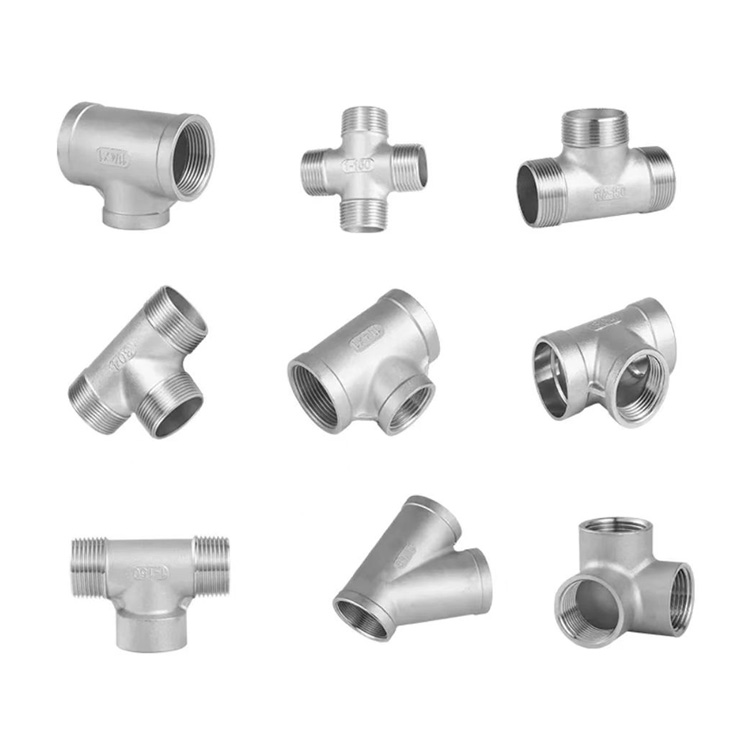
Socket fittings are essential components in piping systems, designed to connect, branch, or...
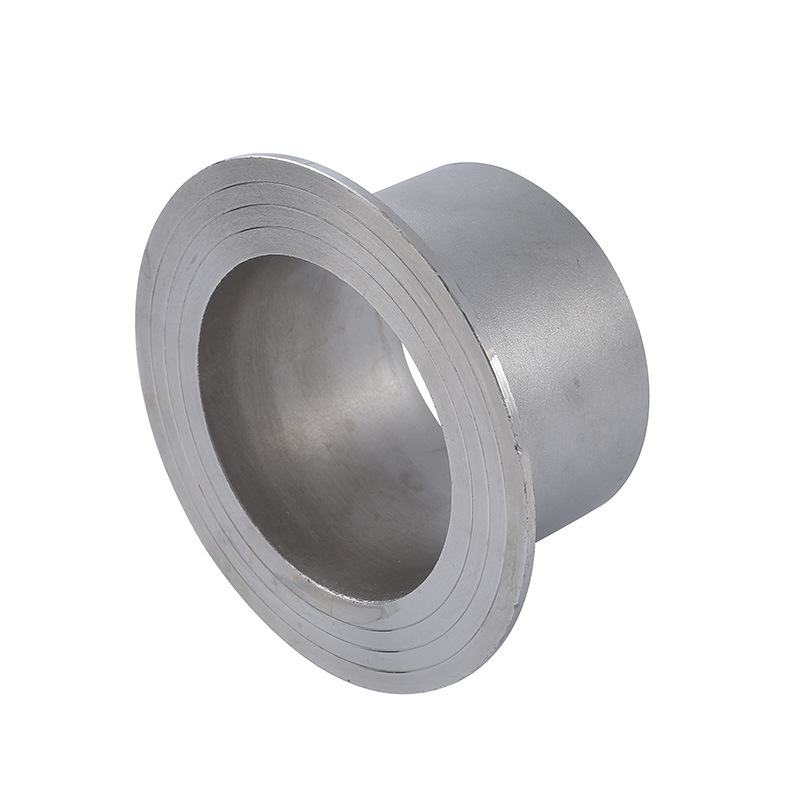
Welding ring is a commonly used metal ring component in pipeline connection or equipment do...
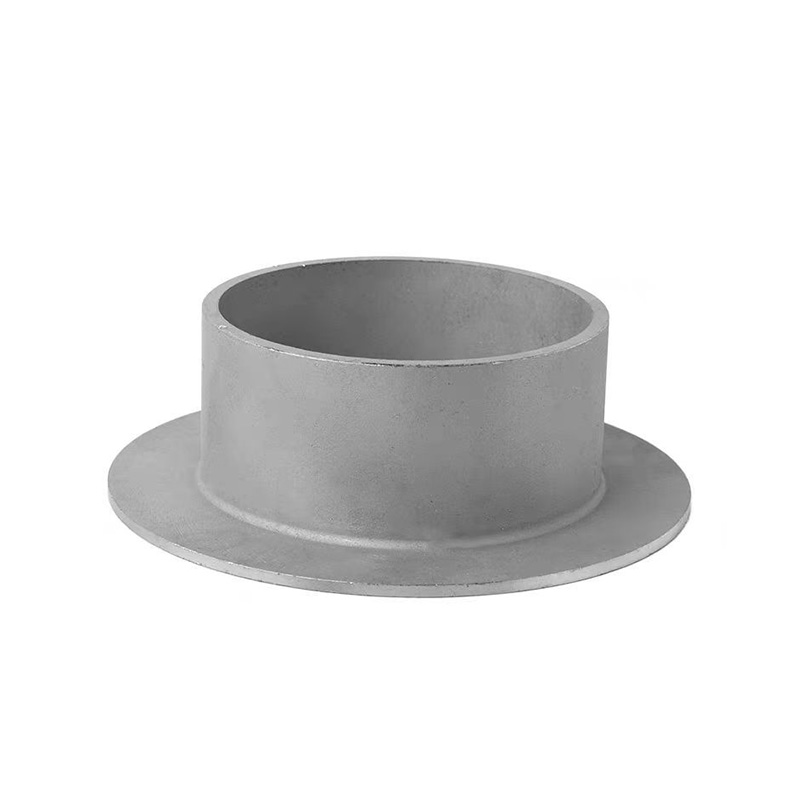
Welding ring is a pipe fitting used for pipeline connection. The following is its detailed ...