Causes and Solutions for Flange Leakage
2025-06-26 17:11:53
Causes and Solutions for Flange Leakage
Flange leakage is a common issue in piping systems, especially in high-pressure and high-temperature environments like those found in the petroleum and chemical industries. Understanding the root causes and applying proper solutions is essential to ensure system integrity and safety.
Common Causes of Flange Leakage:
Improper Gasket Selection:
Using the wrong gasket material or type for the operating conditions (e.g., temperature, pressure, chemical compatibility) can lead to gasket failure and leakage.
Insufficient or Uneven Bolt Tightening:
If flange bolts are not tightened evenly or to the correct torque, it can cause uneven gasket compression, resulting in leaks at certain points.
Flange Surface Damage or Irregularities:
Scratches, dents, warping, or corrosion on the flange face can prevent proper gasket sealing.
Thermal Expansion and Contraction:
Fluctuating temperatures can cause expansion and contraction of piping and flange components, loosening bolts over time or damaging gaskets.
Incorrect Flange Alignment:
If the connected pipes are misaligned, the flange faces may not meet properly, preventing a full seal.
Vibration and Mechanical Stress:
Constant vibration or mechanical loads on the pipeline can gradually loosen the bolts or degrade the gasket, leading to leakage.
Poor Gasket Installation:
Improper placement, reuse of gaskets, or contamination during installation can compromise sealing performance.
Solutions to Prevent and Fix Flange Leakage:
Select the Correct Gasket:
Choose a gasket material compatible with the process fluid, temperature, and pressure. Use metallic or spiral-wound gaskets for high-pressure applications when necessary.
Use Proper Bolt Tightening Techniques:
Apply uniform torque using a calibrated torque wrench and follow a crisscross bolt-tightening pattern. Consider using hydraulic bolt tensioners for large-diameter flanges.
Inspect Flange Faces:
Check for flatness, smoothness, and cleanliness. Repair or replace flanges with damaged sealing surfaces.
Ensure Proper Alignment:
During installation, verify that the flanges are properly aligned and that there’s no pipe stress causing misalignment.
Control Thermal Effects:
Use expansion joints or flexible connections where needed to accommodate thermal movement without stressing the flange connection.
Monitor and Retighten Bolts:
Regularly inspect critical flange joints for signs of loosening, especially in systems subject to vibration or thermal cycling. Retighten bolts if necessary.
Use Anti-Vibration Supports:
Install pipe supports or dampeners to reduce vibration that could affect flange integrity.
Follow Proper Installation Procedures:
Ensure gaskets are handled and installed correctly—never reuse old gaskets, and keep sealing surfaces clean and dry during assembly.
Conclusion:
Flange leakage can usually be prevented through careful material selection, precise installation, regular inspection, and proper maintenance. Addressing the root causes proactively helps maintain system efficiency, reduce downtime, and enhance operational safety.

AWeld Neck Flange (WN Flange)is a type of piping flange designed to be welded to a pipe or ...
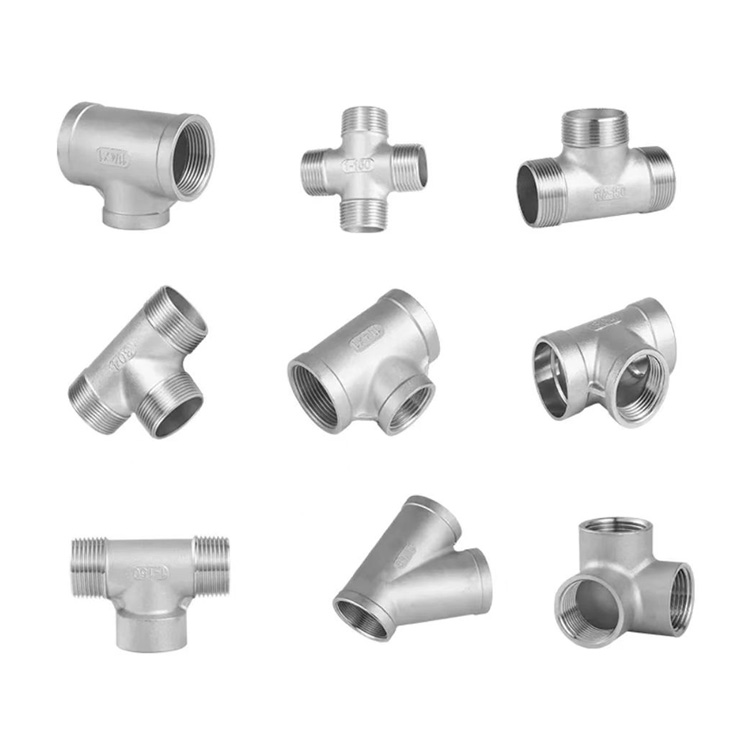
Socket fittings are essential components in piping systems, designed to connect, branch, or...
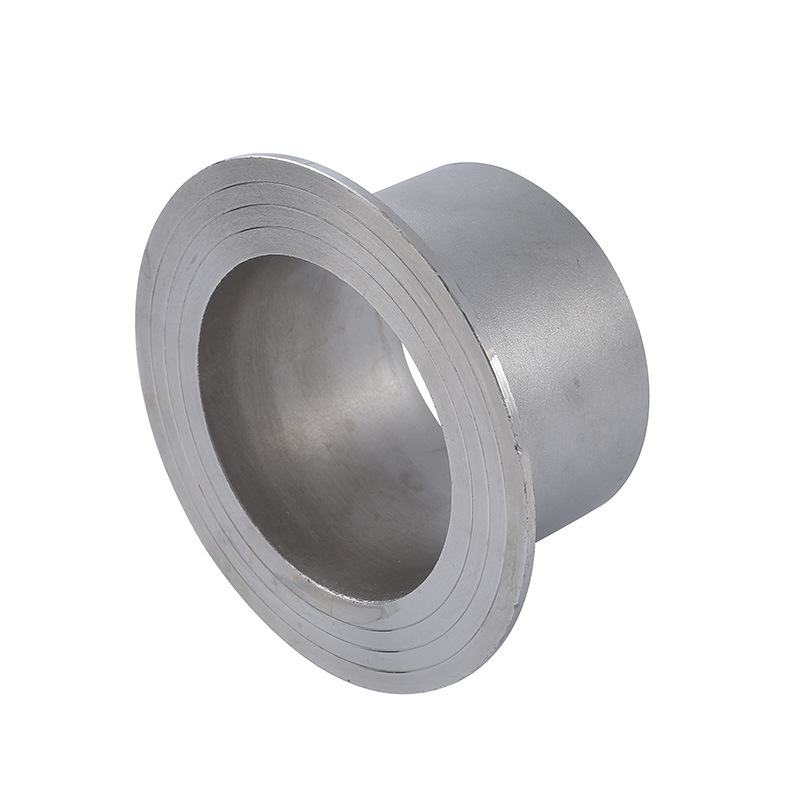
Welding ring is a commonly used metal ring component in pipeline connection or equipment do...
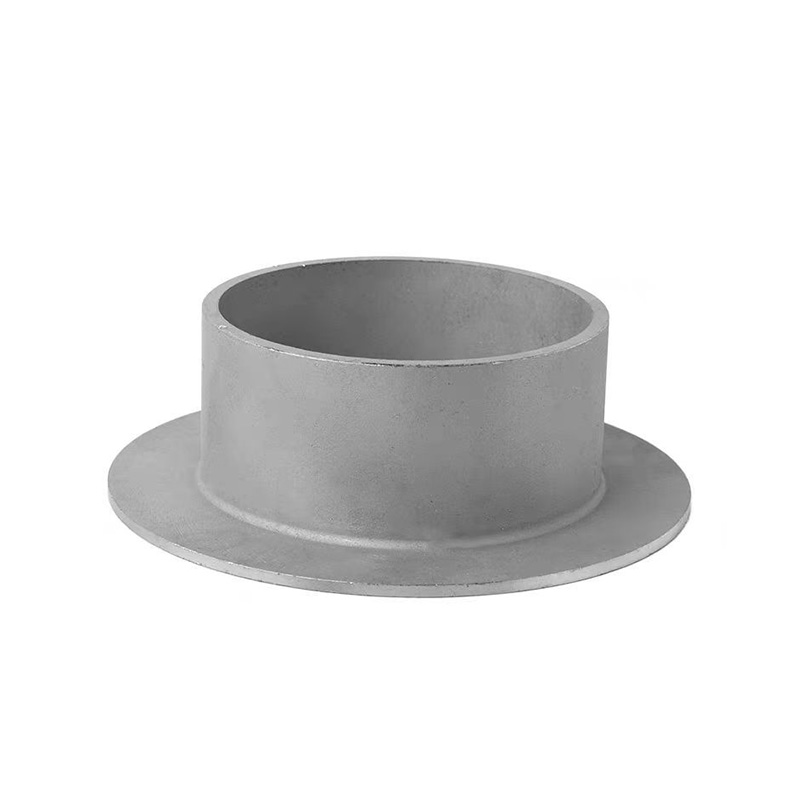
Welding ring is a pipe fitting used for pipeline connection. The following is its detailed ...