Detailed Welding Process of Tee Fittings
2025-06-26 19:22:54
Detailed Welding Process of Tee Fittings
Welding is a critical method for joining tee fittings in industrial piping systems, especially in high-pressure or high-temperature applications. Proper welding ensures mechanical strength, leak tightness, and long-term reliability. Below is a step-by-step explanation of the welding process for tee fittings:
1. Material Preparation
Cleaning: Remove rust, oil, paint, or any contaminants from the welding surfaces of both the tee and the connecting pipes.
Beveling: For butt-welded tees, ensure the ends are beveled according to applicable standards (typically 37.5° for standard butt joints).
Fit-up Check: Dry-fit the tee and pipes to ensure alignment and correct spacing of the root gap (commonly 1.5–3 mm depending on pipe thickness).
2. Welding Method Selection
The most common welding methods include:
SMAW (Shielded Metal Arc Welding): Widely used for carbon steel and alloy steel pipes.
GTAW (TIG Welding): Preferred for thin-walled stainless steel or precise root passes.
GMAW (MIG Welding): Suitable for fast production on clean surfaces.
SAW (Submerged Arc Welding): Used in shop fabrication for large-diameter pipes.
3. Preheating (if required)
For thicker or high-alloy materials, preheating is done to reduce the risk of cracking and hydrogen-induced failures.
Typical preheat temperatures range from 100°C to 300°C depending on material type.
4. Root Pass Welding
Begin with a high-quality root pass to ensure full penetration and strong fusion between the tee and pipe.
GTAW is often used for root pass due to its precise control and minimal spatter.
5. Fill and Cap Passes
Follow the root with several fill passes to build up the weld.
Finish with a cap pass that slightly overlaps the pipe surface to ensure a smooth, flush joint.
Maintain interpass temperature control between each pass to avoid thermal stress.
6. Welding Positions
Depending on the pipe layout, welding may be performed in horizontal (2G), vertical (3G), overhead (4G), or fixed (5G/6G) positions. Skilled welders are required for non-horizontal positions.
7. Post-Weld Heat Treatment (PWHT)
Required for certain materials like carbon steel, alloy steel, and thick-walled sections.
PWHT relieves residual stresses and improves metallurgical properties of the weld zone.
Typically done at 600–700°C for 1–2 hours based on wall thickness.
8. Inspection and Testing
Perform visual inspection for cracks, undercut, porosity, or misalignment.
Conduct non-destructive tests (NDT) such as:
Radiographic Testing (RT): To check internal weld quality.
Ultrasonic Testing (UT): For detecting flaws in thicker materials.
Dye Penetrant Testing (PT): For detecting surface cracks.
Magnetic Particle Testing (MT): For surface/subsurface flaws in ferromagnetic materials.
Hydrostatic or pneumatic pressure testing may follow to ensure leak-proof integrity.
9. Documentation
Record all weld parameters, materials used, welder qualifications, inspection reports, and test results in the welding documentation (WPS/PQR/WQR).
Conclusion
Welding tee fittings is a precision process that demands proper preparation, skilled execution, and thorough inspection. Following established welding procedures and quality control standards ensures strong, leak-free joints that meet the demanding requirements of industrial piping systems.

AWeld Neck Flange (WN Flange)is a type of piping flange designed to be welded to a pipe or ...
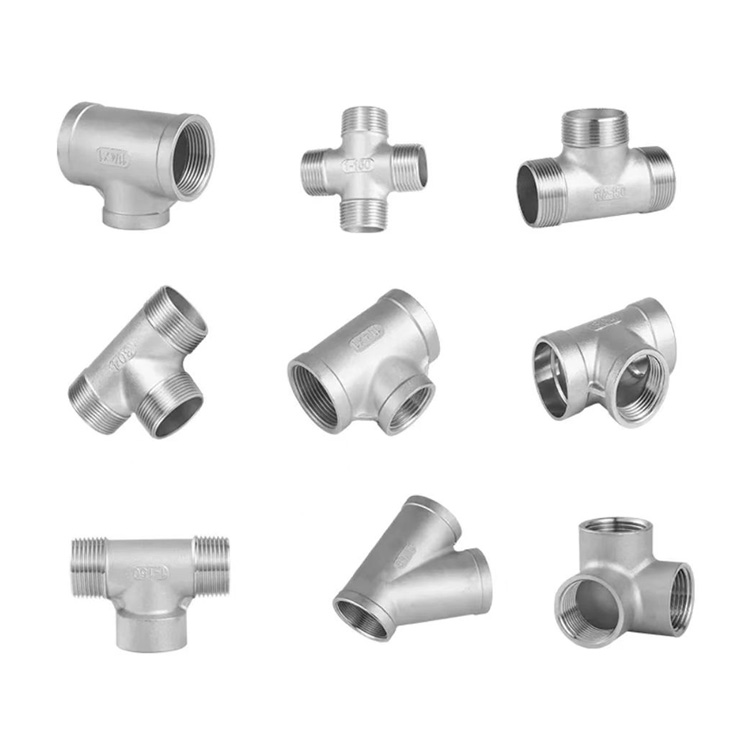
Socket fittings are essential components in piping systems, designed to connect, branch, or...
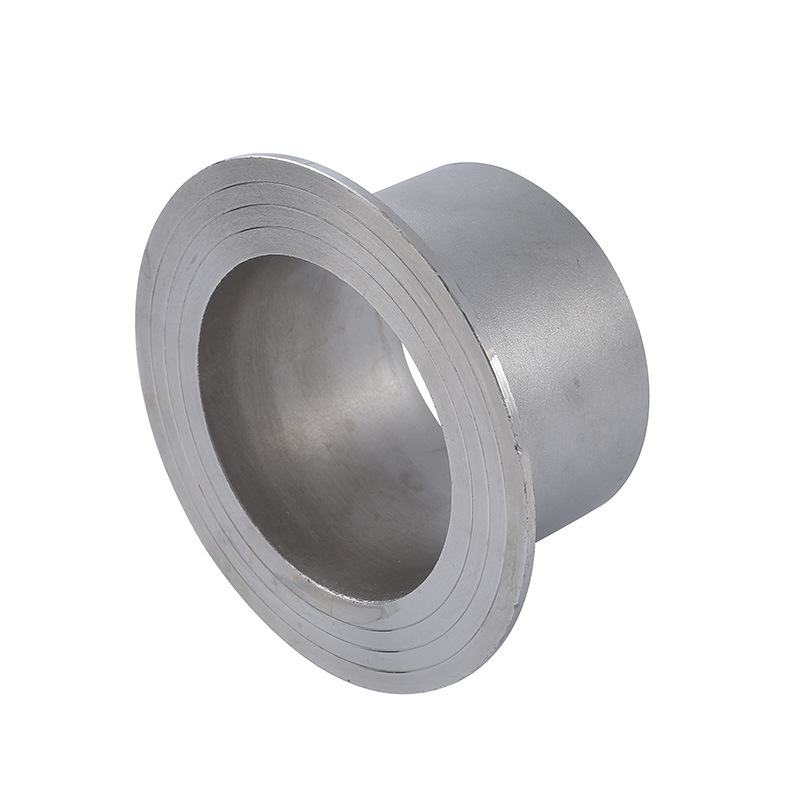
Welding ring is a commonly used metal ring component in pipeline connection or equipment do...
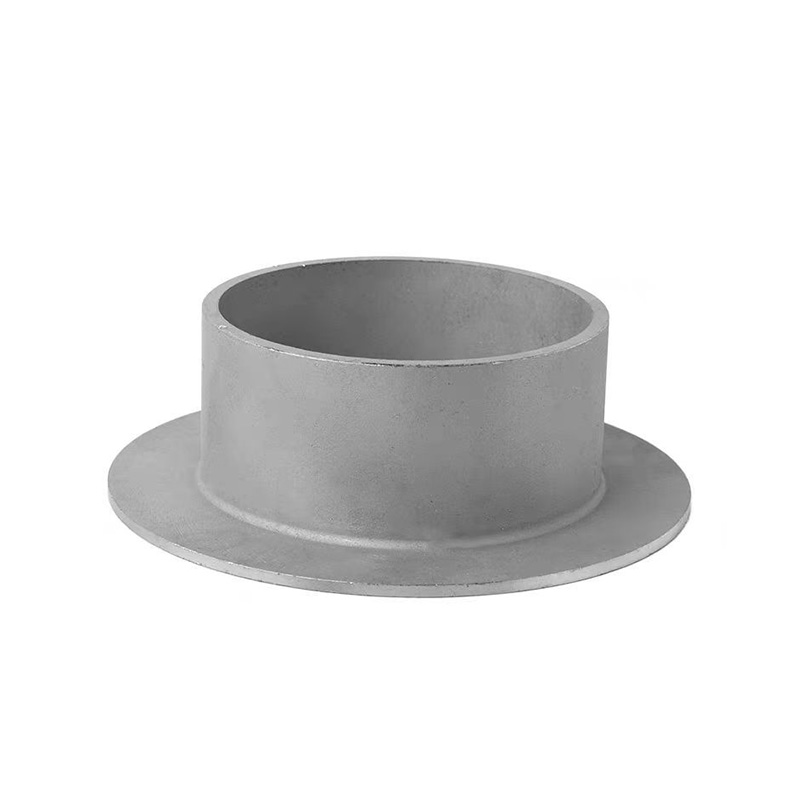
Welding ring is a pipe fitting used for pipeline connection. The following is its detailed ...