Key Points for Transportation and Installation of Large-Diameter Tee Fittings
2025-06-26 19:24:41
Key Points for Transportation and Installation of Large-Diameter Tee Fittings
Large-diameter tee fittings are commonly used in high-capacity industrial pipelines such as oil, gas, water, and chemical transport systems. Due to their size, weight, and complexity, both transportation and installation require careful planning and execution to ensure safety, efficiency, and structural integrity.
1. Transportation Considerations
Proper Packaging and Protection: Use wooden crates, rubber padding, or plastic wrapping to protect the tee from scratches, dents, or corrosion during transit.
Lifting and Handling: Use certified lifting equipment such as slings, cranes, or forklifts. Avoid lifting from branch connections to prevent deformation. Always lift using designated lifting lugs or spreader bars.
Positioning: Support the tee fitting evenly during transportation to prevent bending or stress. Large tees should be placed in a stable, horizontal position with supports under the main run.
Route Planning: Ensure the transport route accommodates the size and weight of the fitting, including bridge and tunnel clearances. Use escort vehicles for oversize loads if necessary.
Marking and Identification: Clearly label the fitting with handling instructions, orientation marks, and identification numbers for easy tracking on site.
2. Installation Preparation
Inspection Before Installation: Check for damage, corrosion, or deformation from transport. Verify dimensions and material certificates match project specifications.
Surface Cleaning: Remove dirt, oil, or protective coatings from the welding or connection areas to ensure proper fit-up and joint integrity.
Support Design: Provide temporary and permanent supports specifically designed for the tee’s size and weight. Improper support can lead to misalignment or joint stress.
Weld Preparation: For welded tees, ensure proper edge preparation (beveling, root gap) and alignment with the connecting pipes.
3. Installation Techniques
Accurate Alignment: Use laser levels or alignment tools to position the tee precisely with the rest of the piping system. Misalignment can cause joint stress and leakage.
Controlled Lifting: During placement, ensure slow and controlled movement to avoid impacting adjacent structures or pipes. Use tag lines to guide the tee into position.
Welding and Jointing: Follow approved welding procedures or bolting methods, depending on the connection type. Perform root, fill, and cap passes with qualified welders.
Support During Welding: Keep the tee securely supported during welding to avoid stress from thermal expansion or misalignment.
Stress Relief Measures: For high-pressure systems or heavy-wall tees, post-weld heat treatment (PWHT) may be required.
4. Final Checks and Testing
Non-Destructive Testing (NDT): Inspect welds using radiography or ultrasonic testing to ensure quality.
Pressure Testing: Conduct hydrostatic or pneumatic pressure tests according to system specifications to confirm leak-proof performance.
Documentation: Record installation steps, test results, and inspection reports for quality assurance and future reference.
Conclusion
Transporting and installing large-diameter tee fittings requires detailed planning, appropriate equipment, and skilled labor. By following best practices for handling, support, welding, and testing, operators can ensure safe and successful integration of these critical components into the piping system.

AWeld Neck Flange (WN Flange)is a type of piping flange designed to be welded to a pipe or ...
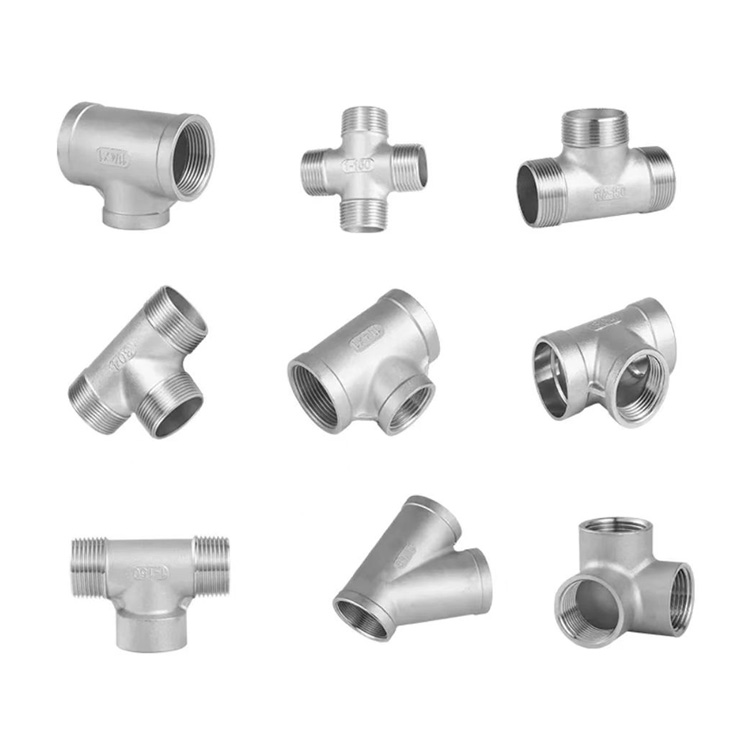
Socket fittings are essential components in piping systems, designed to connect, branch, or...
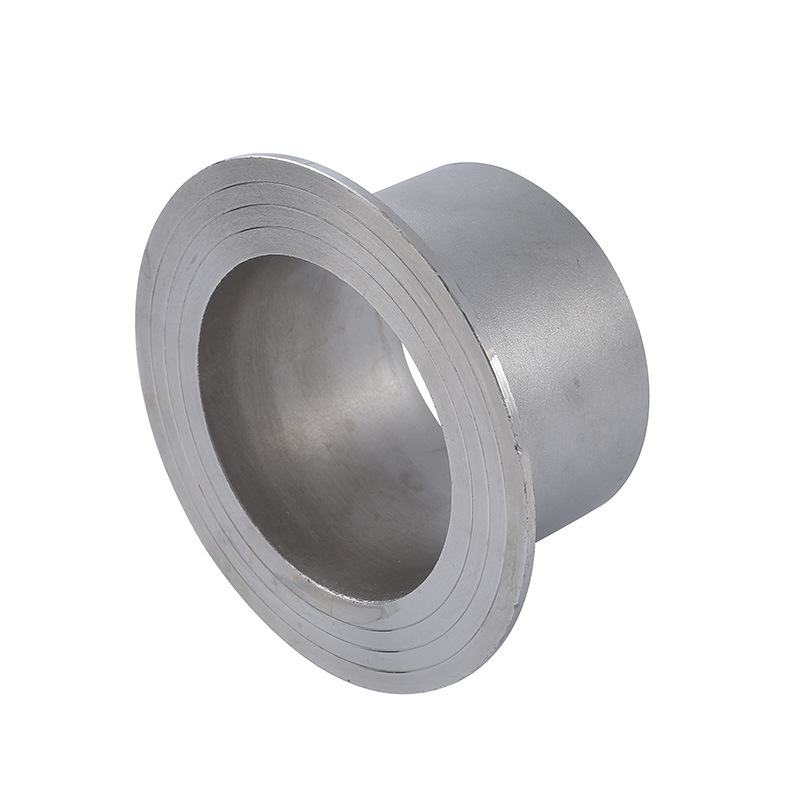
Welding ring is a commonly used metal ring component in pipeline connection or equipment do...
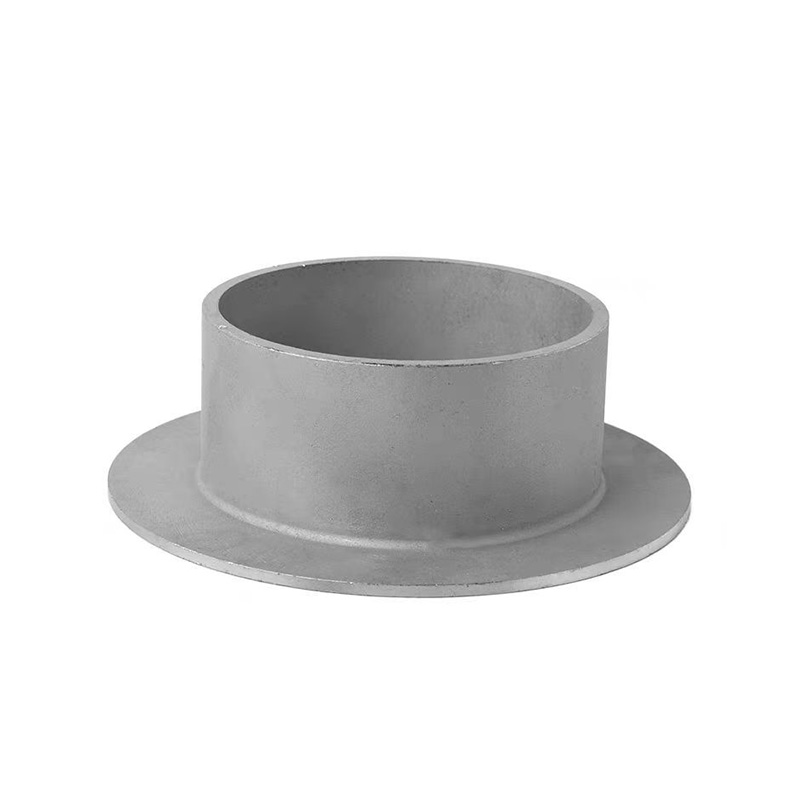
Welding ring is a pipe fitting used for pipeline connection. The following is its detailed ...