Common Welding Defects in Elbows and Their Countermeasures
2025-06-26 19:35:03
Elbows are critical components in piping systems that often undergo welding during installation or fabrication. However, due to their shape and welding complexity, defects can occur, potentially compromising the strength and integrity of the piping system. Below are common welding defects found in elbows and strategies to address them:
1. Cracking
Cause: High residual stress, rapid cooling, improper preheat or post-weld heat treatment (PWHT), or hydrogen embrittlement.
Countermeasures:
Use proper preheating and PWHT according to material specifications.
Control welding parameters to avoid excessive heat input.
Use low-hydrogen welding consumables and ensure a clean welding environment.
Apply controlled cooling after welding.
2. Porosity
Cause: Contamination by moisture, oil, rust, or shielding gas defects.
Countermeasures:
Clean surfaces thoroughly before welding.
Use dry and properly stored electrodes or filler materials.
Ensure adequate shielding gas flow and no drafts in the welding area.
3. Incomplete Penetration or Fusion
Cause: Incorrect welding parameters, poor fit-up, improper beveling, or insufficient heat input.
Countermeasures:
Ensure proper joint preparation with correct bevel angles and root gaps.
Adjust welding current, voltage, and speed for full penetration.
Use qualified welding procedures and trained welders.
4. Undercut
Cause: Excessive welding speed or incorrect electrode angle causing groove along the weld toe.
Countermeasures:
Optimize welding speed and electrode manipulation.
Maintain proper welding angle to avoid sharp edges.
5. Overlap
Cause: Welding filler metal flowing over base metal without bonding.
Countermeasures:
Control welding parameters to ensure proper fusion.
Use correct electrode positioning.
6. Distortion
Cause: Uneven heat input causing metal shrinkage and warping.
Countermeasures:
Use balanced welding techniques and sequence to distribute heat evenly.
Employ clamps or fixtures to hold the elbow in place during welding.
7. Slag Inclusion
Cause: Improper cleaning between weld passes or incorrect welding technique.
Countermeasures:
Clean slag thoroughly after each pass.
Use appropriate welding technique and electrode manipulation.
Conclusion
Addressing welding defects in elbows requires careful attention to welding preparation, parameter control, and post-weld treatment. Following established welding procedures and quality control measures ensures strong, defect-free joints that maintain the integrity of piping systems.

AWeld Neck Flange (WN Flange)is a type of piping flange designed to be welded to a pipe or ...
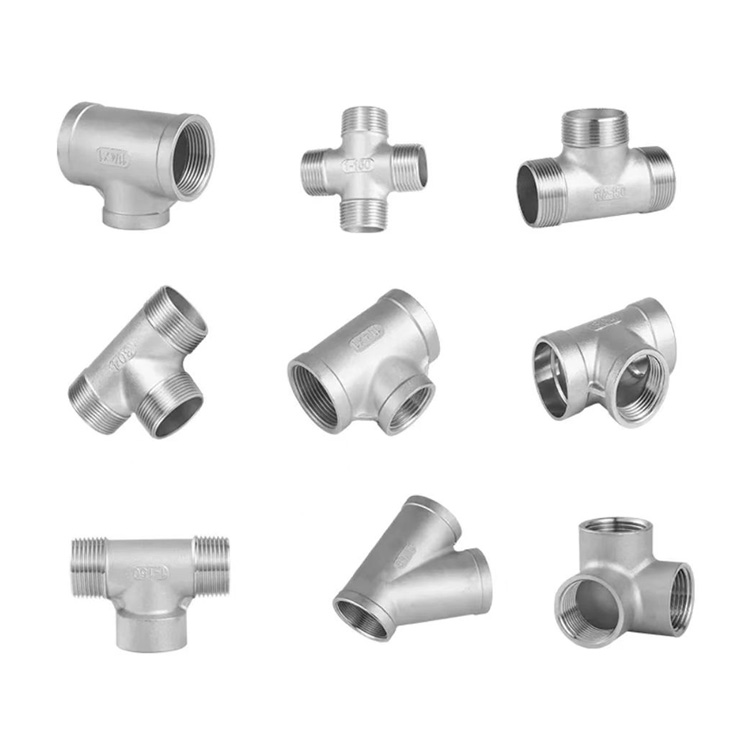
Socket fittings are essential components in piping systems, designed to connect, branch, or...
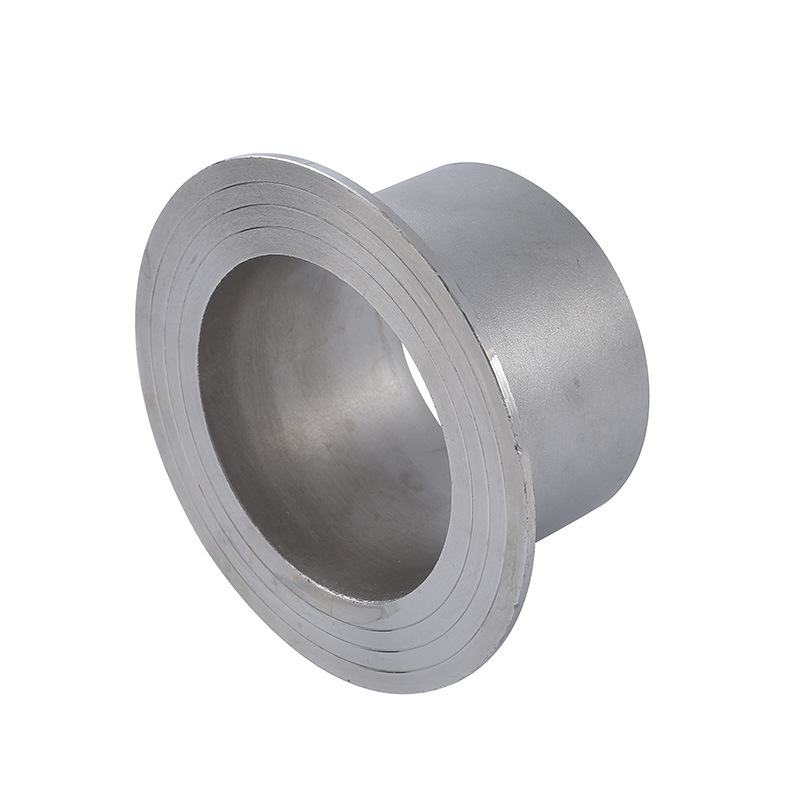
Welding ring is a commonly used metal ring component in pipeline connection or equipment do...
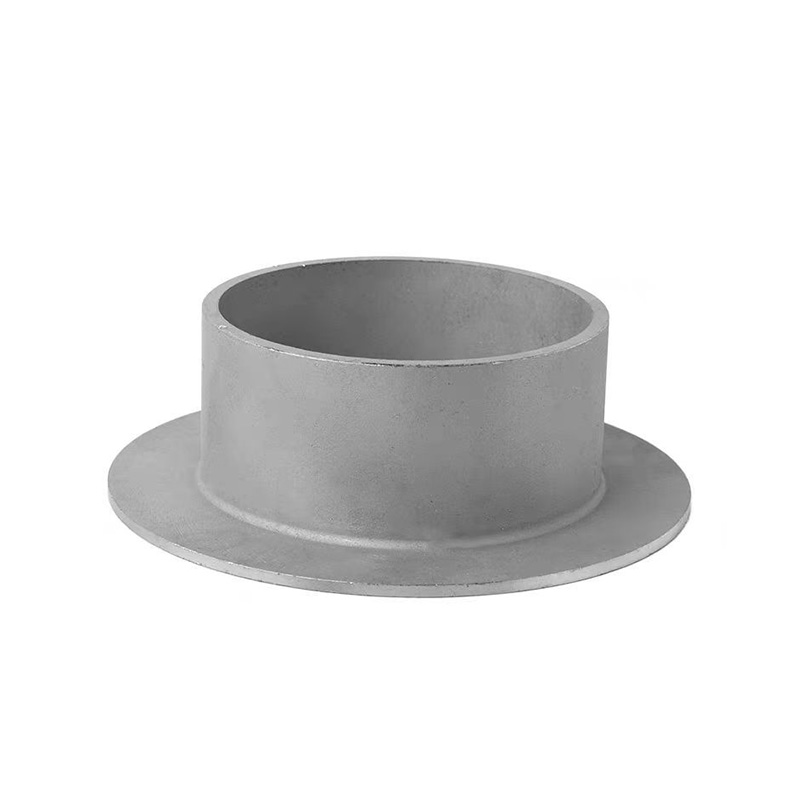
Welding ring is a pipe fitting used for pipeline connection. The following is its detailed ...