Erosion Issues of Elbows in Pneumatic Conveying Systems
2025-06-26 19:35:49
Erosion Issues of Elbows in Pneumatic Conveying Systems
In pneumatic conveying systems, elbows are critical components where airflow direction changes sharply. Due to the high velocity of conveyed particles and abrasive nature of materials, elbows often face significant wear and erosion problems that can affect system performance and longevity.
1. Causes of Elbow Wear in Pneumatic Conveying
Particle Impact: High-speed particles collide with the elbow’s inner surface, especially on the outer radius of the bend, causing material removal.
Abrasive Materials: Conveying abrasive powders, granules, or dust accelerates surface erosion.
Flow Velocity: Higher air velocities increase the kinetic energy of particles, intensifying erosion.
Turbulence and Flow Patterns: Turbulent flow and particle re-circulation zones within the elbow cause uneven wear.
Material Properties: The elbow’s base material hardness and toughness influence wear resistance.
2. Common Wear Patterns
Outer Radius Thinning: The most severe wear typically occurs at the outer curve of the elbow due to direct particle impingement.
Localized Pitting: Small, deep pits can form from repeated impact, potentially leading to leaks.
General Surface Abrasion: Uniform thinning of the elbow wall over time, reducing structural integrity.
3. Mitigation and Protection Strategies
Material Selection: Use wear-resistant materials such as hardened steel, abrasion-resistant alloys, or ceramics for elbows exposed to heavy wear.
Protective Linings: Apply internal coatings like rubber, polyurethane, ceramic tiles, or tungsten carbide overlays to absorb impact and reduce erosion.
Elbow Design:
Opt for long-radius elbows to reduce particle impact angle and velocity against the surface.
Consider installing segmented or replaceable wear liners for easier maintenance.
Flow Control: Reduce conveying velocity where possible without compromising system efficiency to lower wear rates.
Regular Inspection and Maintenance: Monitor elbow thickness and surface condition using ultrasonic testing or visual inspection to plan timely replacements or repairs.
4. System Optimization
Use proper particle size distribution and moisture control to minimize abrasive impact.
Design the conveying system to avoid sharp bends and excessive turbulence.
Conclusion
Wear and erosion in elbows within pneumatic conveying systems are common challenges due to abrasive particle impact and high velocities. Selecting appropriate materials, protective linings, optimized elbow designs, and regular maintenance are key to extending service life and maintaining efficient operation.

AWeld Neck Flange (WN Flange)is a type of piping flange designed to be welded to a pipe or ...
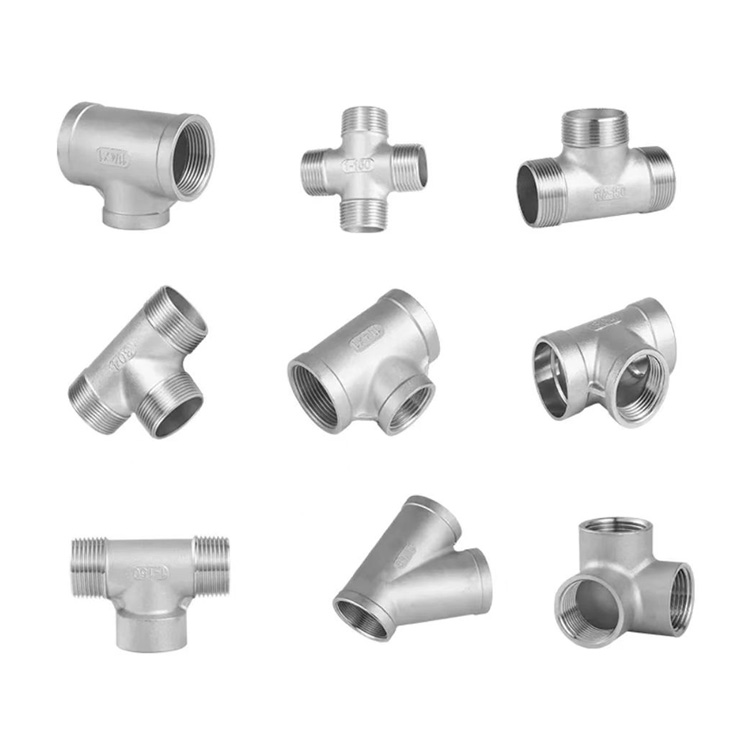
Socket fittings are essential components in piping systems, designed to connect, branch, or...
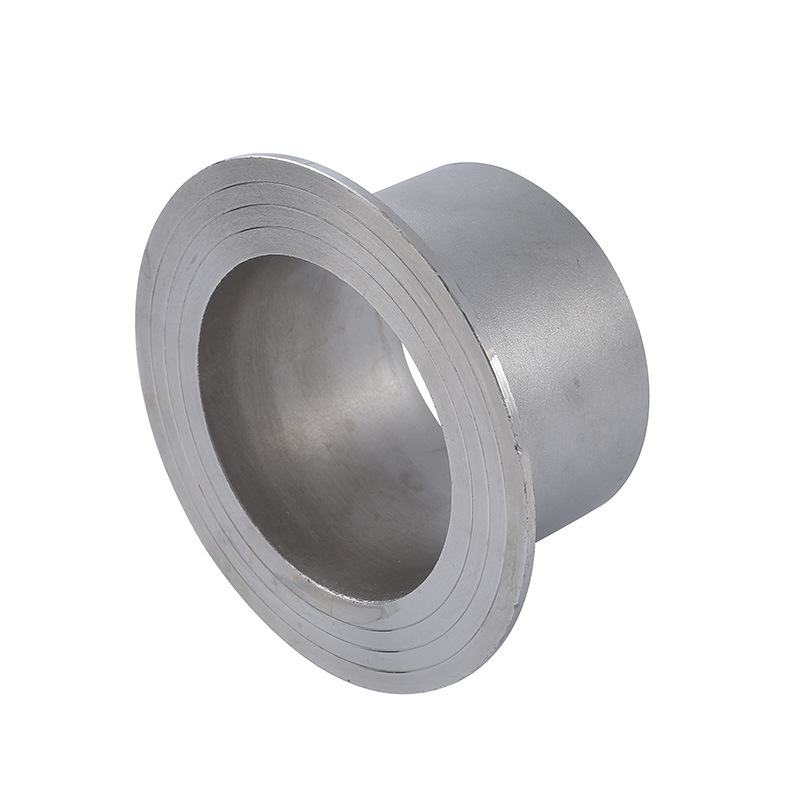
Welding ring is a commonly used metal ring component in pipeline connection or equipment do...
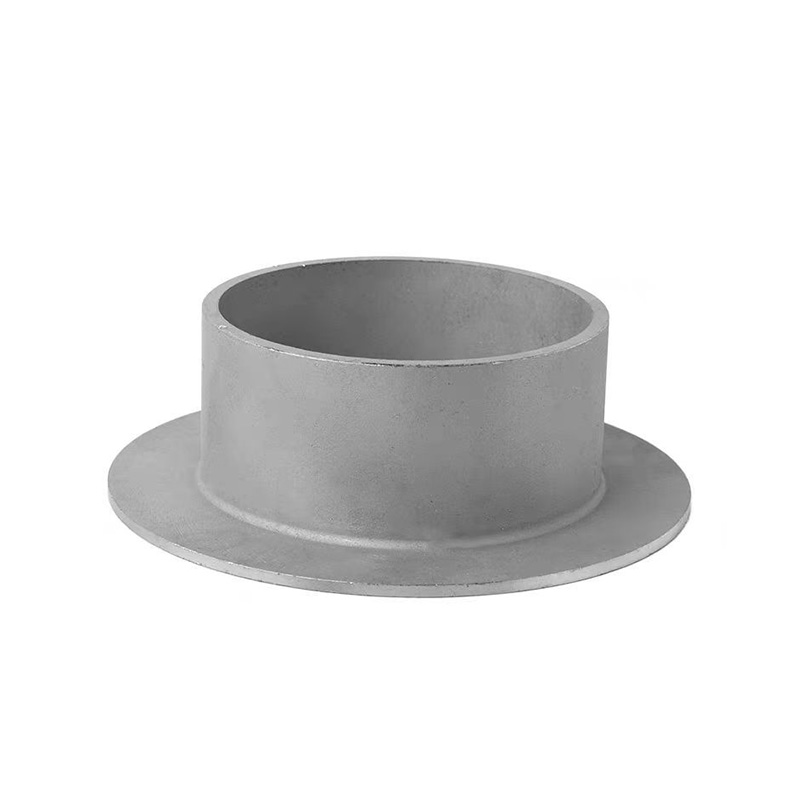
Welding ring is a pipe fitting used for pipeline connection. The following is its detailed ...