What are the precautions for flange design
2025-03-24 16:16:51
Precautions for Flange Design in Petrochemical Pipelines
1. Material Selection
Ensure compatibility between flange material, gasket, and bolting to avoid galvanic corrosion (e.g., carbon steel flanges with stainless steel bolts may require insulation).
Consider fluid corrosivity, temperature, and pressure (e.g., stainless steel for acidic media, alloy steels for high-temperature service).
Verify compliance with standards (ASTM, ASME) for material grades (e.g., A105, A182-F316).
2. Pressure-Temperature Ratings
Select flanges rated for the maximum operating pressure and temperature (refer to ASME B16.5/B16.47 for class ratings: 150#, 300#, etc.).
Account for thermal expansion/contraction effects, especially in high-temperature pipelines.
3. Flange Face Type
Raised Face (RF): Common for general services; ensure proper gasket compression.
Flat Face (FF): Used with cast iron or low-pressure systems; avoid mismatching with RF flanges.
Ring-Type Joint (RTJ): Critical for high-pressure/temperature (HP/HT) applications; requires precision machining.
4. Gasket Selection
Match gasket material to fluid compatibility and temperature (e.g., graphite for high heat, PTFE for acids).
Ensure proper gasket thickness and width to prevent blowout under pressure.
Avoid over-tightening bolts to prevent gasket crushing (follow ASME PCC-1 bolt-torque guidelines).
5. Bolt & Nut Considerations
Use bolts of adequate strength (e.g., ASTM A193-B7 for high stress).
Apply uniform bolt tightening via cross-pattern sequencing to prevent flange distortion.
Consider lubrication on threads to achieve consistent torque.
6. Flange Alignment & Loads
Misalignment causes leakage and stress; ensure parallel mating surfaces during installation.
Avoid excessive external loads (e.g., pipe weight, vibration) by using supports/expansion joints.
For large-diameter flanges, verify flange rigidity to prevent bending under load.
7. Corrosion & Erosion Protection
Apply coatings (e.g., epoxy, galvanization) for corrosive environments.
In erosive services (e.g., slurries), consider hardened materials or protective liners.
8. Standards & Inspection
Adhere to ASME B16.5/B16.47, API, or ISO standards for dimensions and tolerances.
Perform visual and NDT inspections (dye penetrant, ultrasonic) post-welding/installation.
Ensure flange faces are free of scratches or pitting to maintain seal integrity.
9. Special Cases
Insulating Flanges: Required for cathodic protection to prevent stray current corrosion.
Lap-Joint Flanges: Useful for frequent disassembly but require stub-end backing.
Orifice Flanges: Include taps for flow measurement; ensure precise machining.
10. Maintenance & Documentation
Periodically check for leaks, bolt stress relaxation, or gasket degradation.
Maintain records of flange specs, materials, and torque values for traceability.

AWeld Neck Flange (WN Flange)is a type of piping flange designed to be welded to a pipe or ...
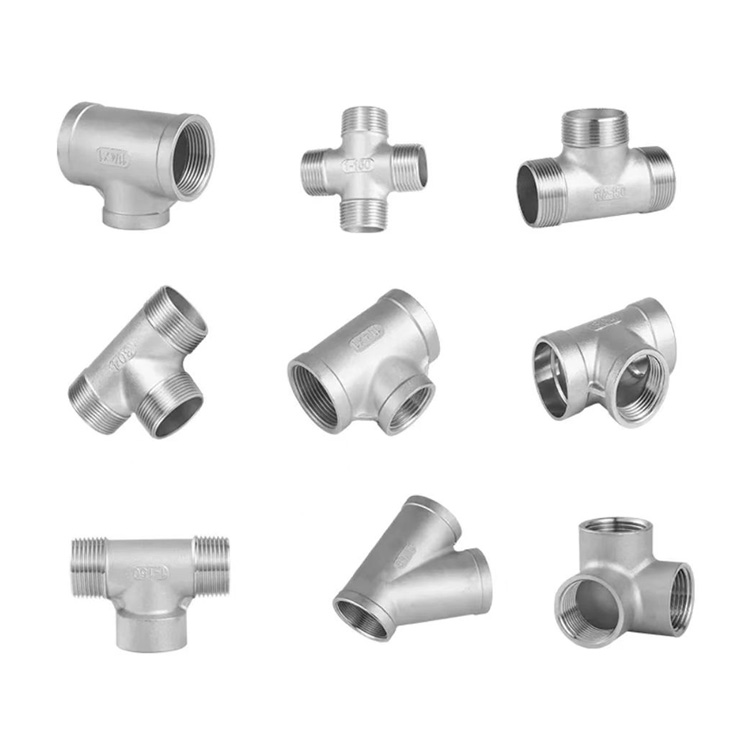
Socket fittings are essential components in piping systems, designed to connect, branch, or...
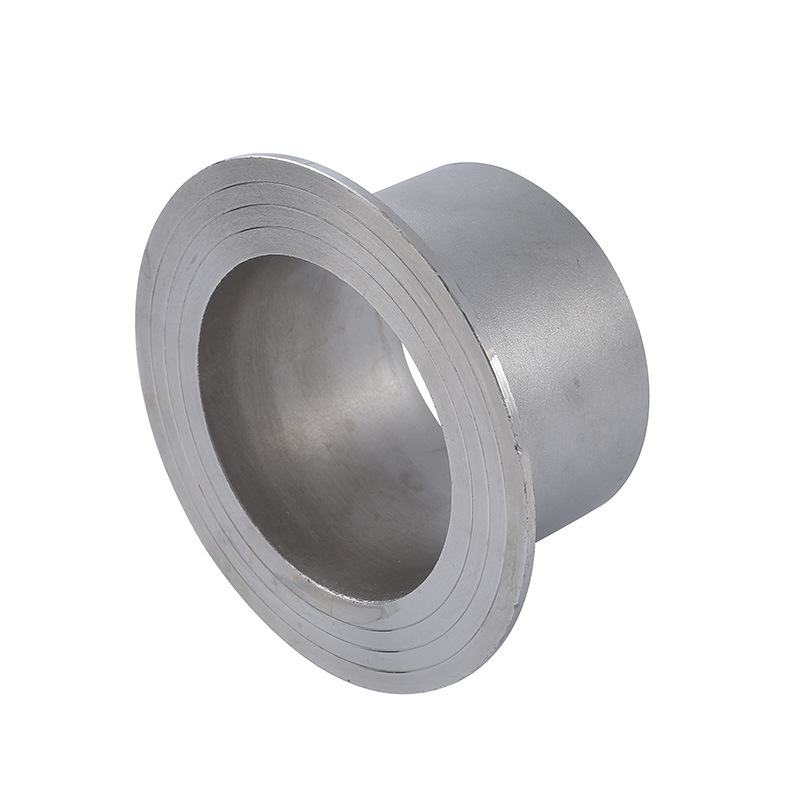
Welding ring is a commonly used metal ring component in pipeline connection or equipment do...
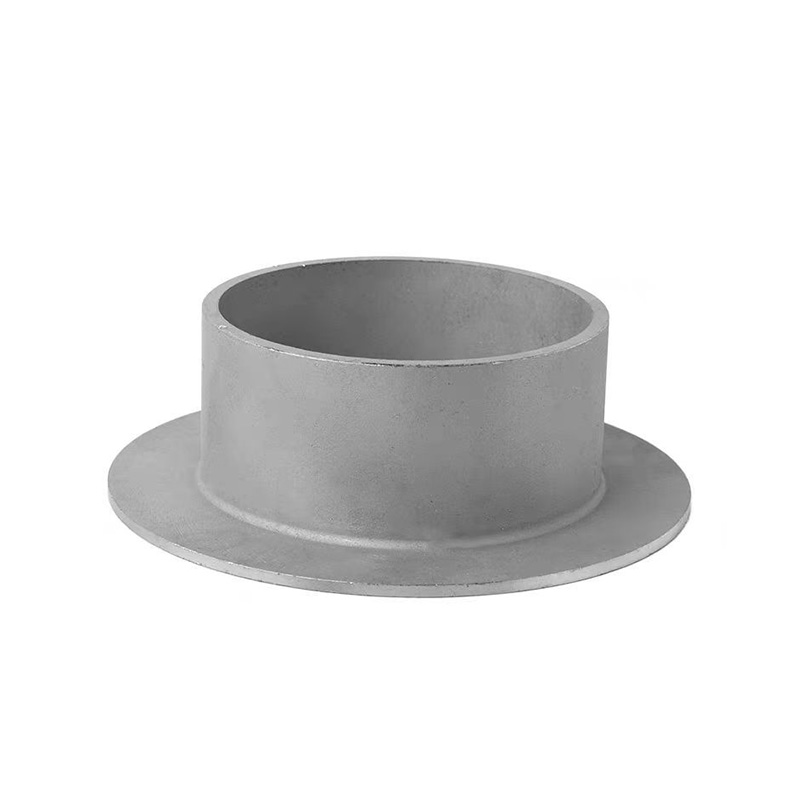
Welding ring is a pipe fitting used for pipeline connection. The following is its detailed ...