Common Issues in Flange Connections of Chemical Piping Systems
2025-06-26 17:30:54
Common Issues in Flange Connections of Chemical Piping Systems
Flange connections are widely used in chemical piping systems due to their ease of assembly and disassembly. However, improper design, installation, or maintenance can lead to various problems that compromise safety, reliability, and performance.
1. Leakage at the Flange Joint:
Leakage is the most common issue and is often caused by improper gasket selection, uneven bolt tightening, flange misalignment, or surface damage. In chemical environments, leaks can pose serious safety and environmental hazards.
2. Gasket Degradation:
Exposure to aggressive chemicals, high temperatures, or excessive compression can degrade gasket material. Using incompatible gasket materials leads to softening, hardening, swelling, or cracking, resulting in loss of sealing function.
3. Bolt Loosening or Failure:
Thermal cycling, vibration, or improper torque can cause bolts to loosen over time. If bolts are over-tightened, they may stretch beyond their elastic limit and fail. Inadequate bolt preload also reduces sealing pressure.
4. Corrosion of Flange and Bolts:
Chemical exposure can lead to corrosion of flange faces and bolts, especially if unsuitable materials are used. Corrosion weakens the connection, causes surface pitting, and affects gasket sealing performance.
5. Misalignment of Flange Faces:
If pipes are not properly aligned before flange connection, the flange faces may not contact evenly. This leads to uneven gasket compression and increases the risk of leaks and mechanical stress on the joint.
6. Gasket Blowout or Extrusion:
Improper installation, under-tightening, or excessive internal pressure can cause the gasket to extrude or blow out from the flange joint. This is particularly dangerous in high-pressure or hazardous chemical applications.
7. Improper Flange Surface Finish:
If the flange face is too smooth or too rough, it can prevent proper gasket grip and sealing. Surface imperfections like scratches or dents can create leak paths, especially in soft gasket materials.
8. Thermal Expansion and Pipe Stress:
In high-temperature systems, thermal expansion can create significant stress on flange connections, leading to flange distortion, bolt loosening, or gasket displacement.
9. Vibration and Mechanical Shock:
Frequent vibration from pumps or process equipment can loosen bolts, cause fatigue in the flange joint, and lead to seal failure.
10. Inadequate Maintenance and Inspection:
Failure to regularly inspect, retighten, or replace worn components results in unnoticed degradation and unexpected failures.
Conclusion:
To avoid common flange connection problems in chemical piping systems, it is essential to select the right materials, use proper installation techniques, and perform routine maintenance. Attention to gasket compatibility, bolt tension, alignment, and corrosion protection plays a key role in ensuring long-term sealing performance and operational safety.

AWeld Neck Flange (WN Flange)is a type of piping flange designed to be welded to a pipe or ...
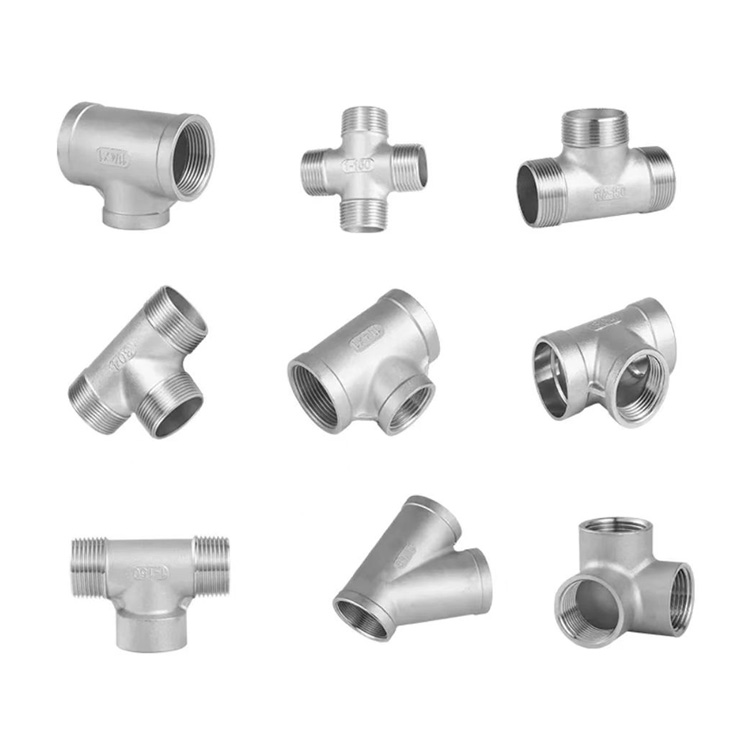
Socket fittings are essential components in piping systems, designed to connect, branch, or...
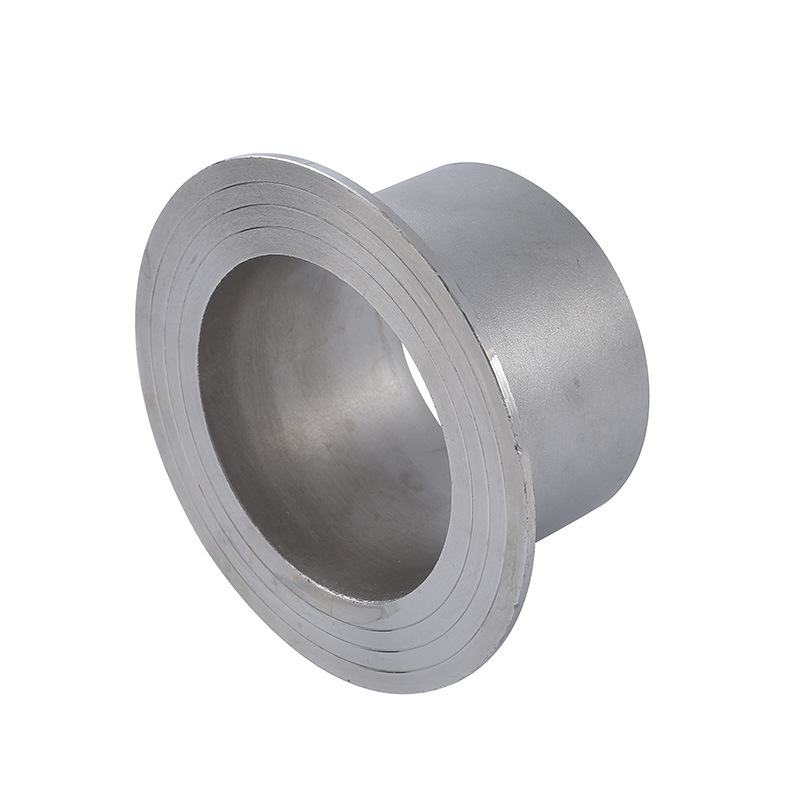
Welding ring is a commonly used metal ring component in pipeline connection or equipment do...
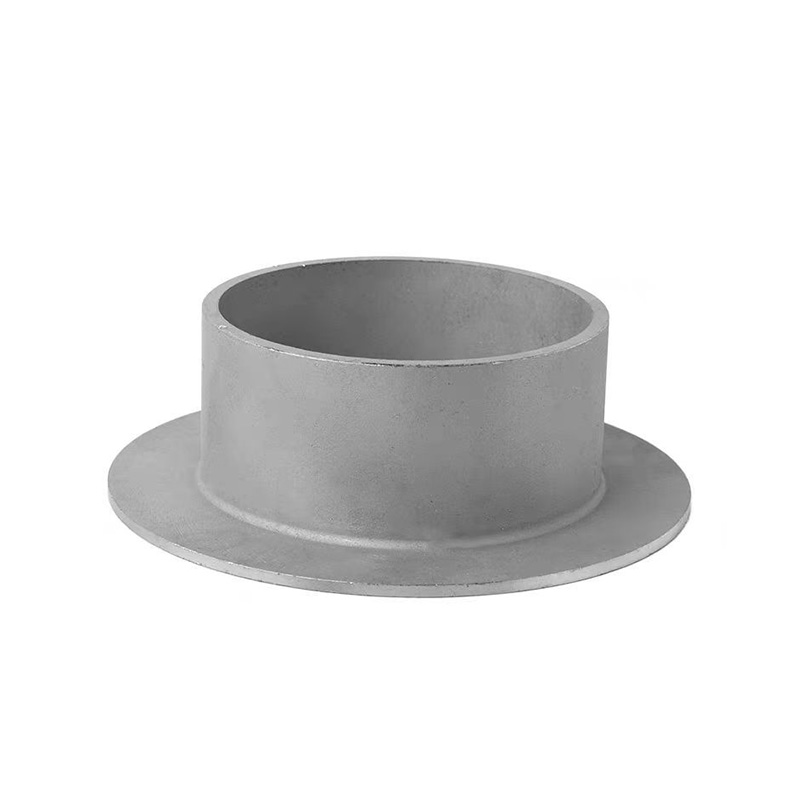
Welding ring is a pipe fitting used for pipeline connection. The following is its detailed ...